Why are electrically insulating heatsinks so rare? Is it just cost? Announcing the arrival of Valued Associate #679: Cesar Manara Planned maintenance scheduled April 23, 2019 at 00:00UTC (8:00pm US/Eastern)Copper or Aluminum Heatsink?Are the non-metallic colored heat sinks of transistor packages electrically isolated/nonconductive?Is there a cheap thermally conductive, electrically insulating potting compound?Why do these two dramatically different sized heatsinks have similar thermal resistance?Why are circuit boards not covered in thermal paste?Why are DIMMs not equipped with a heat sink like a CPU?
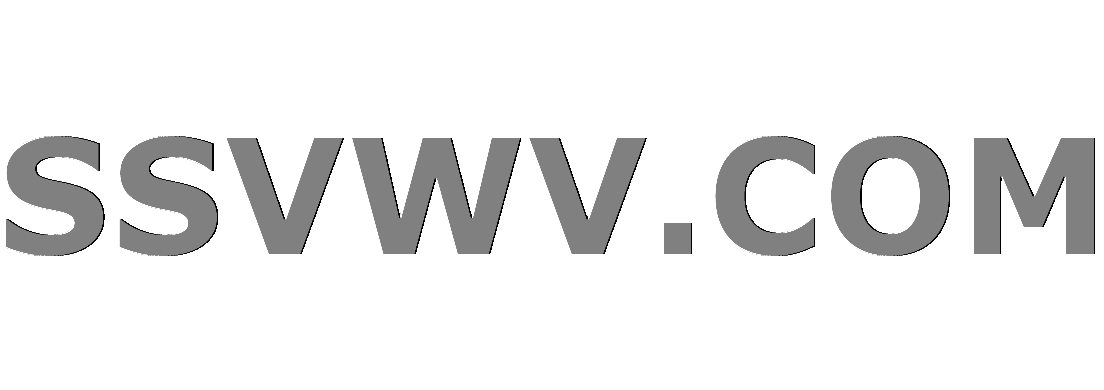
Multi tool use
What happened to Thoros of Myr's flaming sword?
What order were files/directories output in dir?
Is there public access to the Meteor Crater in Arizona?
Sentence with dass with three Verbs (One modal and two connected with zu)
What is Adi Shankara referring to when he says "He has Vajra marks on his feet"?
What does Turing mean by this statement?
One-one communication
A term for a woman complaining about things/begging in a cute/childish way
How many morphisms from 1 to 1+1 can there be?
Project Euler #1 in C++
How to align multiple equations
How does the math work when buying airline miles?
Is it fair for a professor to grade us on the possession of past papers?
How fail-safe is nr as stop bytes?
Do wooden building fires get hotter than 600°C?
In musical terms, what properties are varied by the human voice to produce different words / syllables?
Trademark violation for app?
Semigroups with no morphisms between them
Why can't I install Tomboy in Ubuntu Mate 19.04?
How to dry out epoxy resin faster than usual?
Converted a Scalar function to a TVF function for parallel execution-Still running in Serial mode
Most bit efficient text communication method?
Movie where a circus ringmaster turns people into animals
Crossing US/Canada Border for less than 24 hours
Why are electrically insulating heatsinks so rare? Is it just cost?
Announcing the arrival of Valued Associate #679: Cesar Manara
Planned maintenance scheduled April 23, 2019 at 00:00UTC (8:00pm US/Eastern)Copper or Aluminum Heatsink?Are the non-metallic colored heat sinks of transistor packages electrically isolated/nonconductive?Is there a cheap thermally conductive, electrically insulating potting compound?Why do these two dramatically different sized heatsinks have similar thermal resistance?Why are circuit boards not covered in thermal paste?Why are DIMMs not equipped with a heat sink like a CPU?
.everyoneloves__top-leaderboard:empty,.everyoneloves__mid-leaderboard:empty,.everyoneloves__bot-mid-leaderboard:empty margin-bottom:0;
$begingroup$
Edit: It seems my initial question (Why are there no insulating heatsinks?) was based on a false premise, and there are in fact insulating heatsinks--I just wasn't able to find them with a cursory search. So instead, I'm changing this to ask about their rarity instead.
Heatsinks seem to be almost universally made of aluminum, copper, or some combination thereof. This makes sense; aluminum and copper are easy to work and have high thermal conductivity. But diamond has one of the highest thermal conductivities of any known substance--it's obvious, of course, that diamond of the type suitable for use as a heatsink would be inordinately expensive to say the least, as it would probably have to be a single gem-quality crystal, but would it not be possible to use, for example, cubic boron nitride, which has a similar thermal conductivity?
And yes, the manufacturing difficulties with making a large single crystal of c-BN would probably be about the same as making a large single crystal of diamond, but I expect the end price wouldn't be as much because there's no De Beers group to come after you for boron nitride. And there are surely other nonmetallic compounds that have good heat conductivity, and some of them would presumably be better suited to manufacture. I doubt they'd be able to even approach the price point of extruded aluminum, but sometimes you do need higher performance.
So, in summary, my question is: Is it only cost that makes nonmetallic heatsinks so rare, or are there some other drawbacks that make them less desirable outside of the most esoteric of applications?
thermal heatsink
$endgroup$
|
show 8 more comments
$begingroup$
Edit: It seems my initial question (Why are there no insulating heatsinks?) was based on a false premise, and there are in fact insulating heatsinks--I just wasn't able to find them with a cursory search. So instead, I'm changing this to ask about their rarity instead.
Heatsinks seem to be almost universally made of aluminum, copper, or some combination thereof. This makes sense; aluminum and copper are easy to work and have high thermal conductivity. But diamond has one of the highest thermal conductivities of any known substance--it's obvious, of course, that diamond of the type suitable for use as a heatsink would be inordinately expensive to say the least, as it would probably have to be a single gem-quality crystal, but would it not be possible to use, for example, cubic boron nitride, which has a similar thermal conductivity?
And yes, the manufacturing difficulties with making a large single crystal of c-BN would probably be about the same as making a large single crystal of diamond, but I expect the end price wouldn't be as much because there's no De Beers group to come after you for boron nitride. And there are surely other nonmetallic compounds that have good heat conductivity, and some of them would presumably be better suited to manufacture. I doubt they'd be able to even approach the price point of extruded aluminum, but sometimes you do need higher performance.
So, in summary, my question is: Is it only cost that makes nonmetallic heatsinks so rare, or are there some other drawbacks that make them less desirable outside of the most esoteric of applications?
thermal heatsink
$endgroup$
1
$begingroup$
@crj11 Well! I had looked around for some but didn't encounter that company. They don't give a price, but I suppose it's one of those things where if you have to ask it's too expensive.
$endgroup$
– Hearth
Apr 4 at 13:31
1
$begingroup$
I've used a beryllium oxide washer for this. Problem is that the dust is toxic. You should use gloves and masks on the assembly line to limit exposure to the dust.
$endgroup$
– stark
Apr 4 at 13:45
2
$begingroup$
@Huisman: A lot!
$endgroup$
– Peter Smith
Apr 4 at 13:45
1
$begingroup$
@stark Beryllium oxide? That's somewhat alarming! What drove the decision to use BeO instead of BN or something else less likely to cause injury?
$endgroup$
– Hearth
Apr 4 at 15:21
1
$begingroup$
@Hearth I believe it was a combination of high temp, electrical insulation, thermal conductivity, and mechanical stability. BeO is very stable once in place. Availability of information about other choices was also an issue in pre-internet days.
$endgroup$
– stark
Apr 4 at 17:40
|
show 8 more comments
$begingroup$
Edit: It seems my initial question (Why are there no insulating heatsinks?) was based on a false premise, and there are in fact insulating heatsinks--I just wasn't able to find them with a cursory search. So instead, I'm changing this to ask about their rarity instead.
Heatsinks seem to be almost universally made of aluminum, copper, or some combination thereof. This makes sense; aluminum and copper are easy to work and have high thermal conductivity. But diamond has one of the highest thermal conductivities of any known substance--it's obvious, of course, that diamond of the type suitable for use as a heatsink would be inordinately expensive to say the least, as it would probably have to be a single gem-quality crystal, but would it not be possible to use, for example, cubic boron nitride, which has a similar thermal conductivity?
And yes, the manufacturing difficulties with making a large single crystal of c-BN would probably be about the same as making a large single crystal of diamond, but I expect the end price wouldn't be as much because there's no De Beers group to come after you for boron nitride. And there are surely other nonmetallic compounds that have good heat conductivity, and some of them would presumably be better suited to manufacture. I doubt they'd be able to even approach the price point of extruded aluminum, but sometimes you do need higher performance.
So, in summary, my question is: Is it only cost that makes nonmetallic heatsinks so rare, or are there some other drawbacks that make them less desirable outside of the most esoteric of applications?
thermal heatsink
$endgroup$
Edit: It seems my initial question (Why are there no insulating heatsinks?) was based on a false premise, and there are in fact insulating heatsinks--I just wasn't able to find them with a cursory search. So instead, I'm changing this to ask about their rarity instead.
Heatsinks seem to be almost universally made of aluminum, copper, or some combination thereof. This makes sense; aluminum and copper are easy to work and have high thermal conductivity. But diamond has one of the highest thermal conductivities of any known substance--it's obvious, of course, that diamond of the type suitable for use as a heatsink would be inordinately expensive to say the least, as it would probably have to be a single gem-quality crystal, but would it not be possible to use, for example, cubic boron nitride, which has a similar thermal conductivity?
And yes, the manufacturing difficulties with making a large single crystal of c-BN would probably be about the same as making a large single crystal of diamond, but I expect the end price wouldn't be as much because there's no De Beers group to come after you for boron nitride. And there are surely other nonmetallic compounds that have good heat conductivity, and some of them would presumably be better suited to manufacture. I doubt they'd be able to even approach the price point of extruded aluminum, but sometimes you do need higher performance.
So, in summary, my question is: Is it only cost that makes nonmetallic heatsinks so rare, or are there some other drawbacks that make them less desirable outside of the most esoteric of applications?
thermal heatsink
thermal heatsink
edited Apr 4 at 15:02


laptop2d
27.9k123786
27.9k123786
asked Apr 4 at 13:25
HearthHearth
5,21611340
5,21611340
1
$begingroup$
@crj11 Well! I had looked around for some but didn't encounter that company. They don't give a price, but I suppose it's one of those things where if you have to ask it's too expensive.
$endgroup$
– Hearth
Apr 4 at 13:31
1
$begingroup$
I've used a beryllium oxide washer for this. Problem is that the dust is toxic. You should use gloves and masks on the assembly line to limit exposure to the dust.
$endgroup$
– stark
Apr 4 at 13:45
2
$begingroup$
@Huisman: A lot!
$endgroup$
– Peter Smith
Apr 4 at 13:45
1
$begingroup$
@stark Beryllium oxide? That's somewhat alarming! What drove the decision to use BeO instead of BN or something else less likely to cause injury?
$endgroup$
– Hearth
Apr 4 at 15:21
1
$begingroup$
@Hearth I believe it was a combination of high temp, electrical insulation, thermal conductivity, and mechanical stability. BeO is very stable once in place. Availability of information about other choices was also an issue in pre-internet days.
$endgroup$
– stark
Apr 4 at 17:40
|
show 8 more comments
1
$begingroup$
@crj11 Well! I had looked around for some but didn't encounter that company. They don't give a price, but I suppose it's one of those things where if you have to ask it's too expensive.
$endgroup$
– Hearth
Apr 4 at 13:31
1
$begingroup$
I've used a beryllium oxide washer for this. Problem is that the dust is toxic. You should use gloves and masks on the assembly line to limit exposure to the dust.
$endgroup$
– stark
Apr 4 at 13:45
2
$begingroup$
@Huisman: A lot!
$endgroup$
– Peter Smith
Apr 4 at 13:45
1
$begingroup$
@stark Beryllium oxide? That's somewhat alarming! What drove the decision to use BeO instead of BN or something else less likely to cause injury?
$endgroup$
– Hearth
Apr 4 at 15:21
1
$begingroup$
@Hearth I believe it was a combination of high temp, electrical insulation, thermal conductivity, and mechanical stability. BeO is very stable once in place. Availability of information about other choices was also an issue in pre-internet days.
$endgroup$
– stark
Apr 4 at 17:40
1
1
$begingroup$
@crj11 Well! I had looked around for some but didn't encounter that company. They don't give a price, but I suppose it's one of those things where if you have to ask it's too expensive.
$endgroup$
– Hearth
Apr 4 at 13:31
$begingroup$
@crj11 Well! I had looked around for some but didn't encounter that company. They don't give a price, but I suppose it's one of those things where if you have to ask it's too expensive.
$endgroup$
– Hearth
Apr 4 at 13:31
1
1
$begingroup$
I've used a beryllium oxide washer for this. Problem is that the dust is toxic. You should use gloves and masks on the assembly line to limit exposure to the dust.
$endgroup$
– stark
Apr 4 at 13:45
$begingroup$
I've used a beryllium oxide washer for this. Problem is that the dust is toxic. You should use gloves and masks on the assembly line to limit exposure to the dust.
$endgroup$
– stark
Apr 4 at 13:45
2
2
$begingroup$
@Huisman: A lot!
$endgroup$
– Peter Smith
Apr 4 at 13:45
$begingroup$
@Huisman: A lot!
$endgroup$
– Peter Smith
Apr 4 at 13:45
1
1
$begingroup$
@stark Beryllium oxide? That's somewhat alarming! What drove the decision to use BeO instead of BN or something else less likely to cause injury?
$endgroup$
– Hearth
Apr 4 at 15:21
$begingroup$
@stark Beryllium oxide? That's somewhat alarming! What drove the decision to use BeO instead of BN or something else less likely to cause injury?
$endgroup$
– Hearth
Apr 4 at 15:21
1
1
$begingroup$
@Hearth I believe it was a combination of high temp, electrical insulation, thermal conductivity, and mechanical stability. BeO is very stable once in place. Availability of information about other choices was also an issue in pre-internet days.
$endgroup$
– stark
Apr 4 at 17:40
$begingroup$
@Hearth I believe it was a combination of high temp, electrical insulation, thermal conductivity, and mechanical stability. BeO is very stable once in place. Availability of information about other choices was also an issue in pre-internet days.
$endgroup$
– stark
Apr 4 at 17:40
|
show 8 more comments
8 Answers
8
active
oldest
votes
$begingroup$
One thing that other answers don't seem to have covered is that you only need a very thin layer of electrical insulator (at modest voltages) while the heat spreader part of a heat sink works best if it's thick. So it's more efficient to use a thin electrically-insulating barrier followed by a thick, cheap, and easily-made metal heatsink than it would be to use a single piece of a material that's thermally conductive and electrically insulating. The few materials that do exist (such as diamond) can't be extruded or otherwise easily formed into a heatsink shape. Some can be sintered but sintering can't generally reach the thermal conductivity of bulk material. The engineering effect of all this materials science is that we end up doing what we've always done.
Another factor is stock policies: by stocking bulky robust heatsinks and a smaller number (as they're not always required) of small delicate insulating pads your stock occupies less storage space and capital than if you stocked two types of bulky heatsink. Cost and performance are both better without the insulator when it's not required.
$endgroup$
10
$begingroup$
Now you've got me thinking that "extruded diamond" would be a good bit of technobabble in a sci-fi novel.
$endgroup$
– Hearth
Apr 4 at 21:48
$begingroup$
Chris thickness helps heat flow away from the interface but at the interface surface area, thinner is better for thermal resistance but electrically thicker is better so they are conflicting requirements and the product of thermal and electrical resistance is the figure of merit needed but then puncture resistance is a third factor with surface roughness. all of which makes Mica good but also hard anodized with grease
$endgroup$
– Sunnyskyguy EE75
Apr 5 at 2:38
$begingroup$
@Sunnyskyguy if the heatsink is made of one material, thicker is always better. An interface layer of not great thermal material needs to be thin
$endgroup$
– Chris H
Apr 5 at 7:24
$begingroup$
... Or rather, thicker is always better for the spreader plate part that distributes the heat to the fins
$endgroup$
– Chris H
Apr 5 at 8:47
$begingroup$
The question here is about the Electrical insulating thermal conducting interface rather than the heat spreader. The product of these two conflicting parameters (of thermal and dielectric impedance) is what makes it rare which has conflicting requirements for this layer to be thermally thin and electrically thick. So the heat spreader after this layer is not relevant to the question yet important overall
$endgroup$
– Sunnyskyguy EE75
Apr 5 at 16:14
|
show 2 more comments
$begingroup$
This is hardly a new problem; those of us of a certain age remember the heatsinks with mica insulators for the TO-220 and TO-3 packages.
The issue (at the time) was both material cost and availability and materials science. We have come a long way in our understanding of thermal conductivity of various compounds over the years, but it is still relatively new technology (there are things such as thermally conductive pads that have been around for decades but are not really heat sinks in their own right).
The TO-220 has the heat spreader on the collector / drain of the device, which is usually at an elevated voltage, so the typical arrangement used this technique:
Source.
It was not unusual to use some thermal paste as well to maximise the heat transfer.
Now that does not really explain the relative rarity of integrated insulated heatsinks; that really comes down to 'is it necessary' or can I simply use the well known method of a heat sink and an electrically insulating barrier material which is less expensive (at least, it is today).
The old tried and true method has served well for many decades, but for some applications (particularly those in small devices) such a solution may well not fit.
There are quite a few offerings available, but they tend to be a bit more expensive (on a per watt basis). There is also a lot of research into other materials.
Of course, for the bling factor, you could use these.
So it comes down to a number of things and cost is a major driver. I will also note that a large market for heat sinks is for CPUs and GPUs where the case of the IC is electrically insulated anyway.
$endgroup$
add a comment |
$begingroup$
Polymer heatsinks deserve a mention. Polymer heatsinks aren't that uncommon. I come across polymer heat sinks industrial, automotive, prosumer goods once in a while. They are often hard to recognize as heatsinks, because they can have a second mechanical purposes (an enclosure, a bracket, a reflector of a lamp). These heat sinks are always custom injection-molded parts.
Polymers have a small heat conductivity, compared to any metal. This prompts a question: how can a polymer make an acceptable heatsink? In some cases, the thermal resistance of the heatsink becomes dominated by transfer from heatsink to air, rather than by conduction within the heatsink itself. This can happen when dumping heat into air with natural convection. In these cases, a heatsink made of a special polymer with a relatively high thermal conduction ( $ mathrm20 frac W mcdot K $ ) can be comparable to an aluminium ( $ mathrm200 frac W mcdot K $ ) heatsink with the same geometry.
E2 is the plastic (source)
Some additional discussion in this old answer.
$endgroup$
6
$begingroup$
On first thought, a polymer heat sink seems inefficient due to poor heat conductivity. However, its emissivity is much higher than most metals so what it lacks in conductivity it partly makes up for in radiative cooling. Disclaimer: i work for a company which produces a polymer compound for such applications.
$endgroup$
– nluigi
Apr 4 at 20:00
3
$begingroup$
@user71659 For a while, I though so too. Then I had a chance to ask one company who sells thermally conductive polymer. Their answer had surprised me. It wasn't a relatively common polymer with a thermally conductive solid filler. The polymer itself was thermally conductive. They didn't divulge what family of polymer it was. A problem with solid fillers is that it makes a plastic more viscous and difficult to injection mold (especially when there's a lot of filler by volume).
$endgroup$
– Nick Alexeev♦
Apr 5 at 0:18
1
$begingroup$
@NickAlexeev I suspect they're just trying to pull marketing BS on you. Thermally conductive polymers are filled, see this manufacturer, and 3M's fillers
$endgroup$
– user71659
Apr 5 at 0:41
1
$begingroup$
Unfilled epoxy has ~10x the TC of air so in a situation where convection isn't your friend even that can help. Filled epoxies(https://www.masterbond.com/properties/thermally-conductive-epoxy-adhesives) are a couple of orders of magnitude better. The casting method makes a difference too as epoxy-casting at atmospheric pressure tends to include bubbles of air, making for a much worse TC; a vacuum approach (where suitable) helps with that. [Filled nylon is another approach
$endgroup$
– Chris H
Apr 5 at 8:31
1
$begingroup$
@nluigi So that would make them good for applications where you're expecting a fairly constant amount of heat to remove with limited space which probably applies to many non-mechanical cases - but in cases where you have sudden large amounts but for a relatively short time, it would fail. Interesting. Never thought about heatsinks in this way!
$endgroup$
– UKMonkey
Apr 5 at 11:07
|
show 2 more comments
$begingroup$
The thing about a heat sink is that there are only really two ways to ultimately dispose of the heat, conduction and radiation.
So ultimately, assuming your emmisivity is reasonably close to 1 (Only really matters if you can run HOT, power loss to radiation is 4th power of absolute temperature), and you can make the thing have good thermal contact with the surrounding cooling media (Air, water, whatever), what you make it from only matters a little (That interface is the killer for performance, not the bulk thermal conductivity of the heatsink).
Now clearly you need to design the heatsink so that heat travels thru it reasonably efficiently and in the area where there is a lot of power flux density that might argue for something other then ally, for the bulk of the thing where you have plenty of metal to keep delta T low, cheapest is best.
For a heat spreader or insulating washer it is different of course, heat spreaders by definition are used where the power flux density is very high and minimal thermal resistance is a very good thing, hence the usual use of copper in this role.
For the insulator you do see exotic materials used, because a good thermal conductor that is also an electrical insulator is not that common, so Boron Nitride, Alumina, Beryllium Oxide(!) and the like all see service here, and I would not be shocked by someone using diamond (Probably in some weird RF device).
$endgroup$
$begingroup$
What I'm getting from this is that it's generally better to have a small insulating interface between the device and a metal heatsink, rather than making the entire heatsink insulating, is that correct? That would make sense, and probably meets the needs of most cases where insulated heatsinks would be needed.
$endgroup$
– Hearth
Apr 4 at 13:54
1
$begingroup$
More that thermally conducting but electrically insulating materials are generally less thermally conducting then metals (and more expensive/harder to machine), so the best tradeoff is usually to use the cheap, easy metal for the big bit. This is something of a compromise as it adds at least one thermal junction which adds resistance, but all engineering is compromise.
$endgroup$
– Dan Mills
Apr 4 at 13:57
$begingroup$
Diamond is four times more thermally conductive that any other material. So diamond über alles.
$endgroup$
– jonk
Apr 4 at 14:34
$begingroup$
Also should mention convection heat removal. Different from radiation and conduction. It is kind of related to conduction, though you already knew that :)
$endgroup$
– Marla
Apr 4 at 14:49
1
$begingroup$
Diamond is certainly used as an electrically-insulating, thermally-conducting layer inside experimental RF devices (and weird ones if that's how you refer to GaN). Here's a paper by some current and former colleagues of mine - spoiler: thin layers of diamond aren't great; you get nanocrystals with relatively poor thermal conductivity
$endgroup$
– Chris H
Apr 4 at 15:57
|
show 4 more comments
$begingroup$
From a technical standpoint its certainly possible to manufacture heatsinks with built in isolator pads. The reason they don't do it is economics.
Between the different mechanical, electrical, and thermal choices there are a lot of different combinations. If the isolator and heatsink were one part then the vendors would have to stock a lot more unique part numbers.
By factoring out the isolator and heat sink into unique products the user has a lot more choices.
Here are some of the things to consider.
1) In many cases the user will use gap pads between heat-sinks and hot components to pick up slack in mechanical tolerances. This means that each user will want the pad to be a different thickness.
2) Thermal isolator pad materials vary in how well they are able to conform to rough surfaces. There is often a trade between how squishy the material is and how well it conducts heat.
3) Different users will have different isolation requirements in terms of voltage. There is a trade off between isolation voltage, the material thickness and the thermal resistance.
3) Adding an insulator between a heat-sink and a part has a penalty in terms of thermal resistance. If its possible to not use an insulating layer then you will get the best thermal performance in that case.
$endgroup$
$begingroup$
While this is a good answer, the question I asked was more about heatsinks made entirely of one electrically-insulating substance--not ones with an insulator attached to them.
$endgroup$
– Hearth
Apr 4 at 21:45
add a comment |
$begingroup$
The best compromise is to make an extremely thin large surface area layer with a high rated Voltage [kV/mm] with sufficient hardness to not be cut or punctured but must also be low cost.
Thermally conductive insulator characteristics include;
Cost-effective
Resistant to tears and cut-through
High dielectric strength
UL94 VO rated options available
Low ageing rate: Pads do not dry out, ooze out or crack
Gap Filling, if burrs, roughness or planarity is a problem
Compatibility (gas sensors must be non-silicone and LED interfaces must be non-organic)
Low dielectric constant for capacitance load on collector/drain tabs on high dV/dt high voltage drivers
All electrical insulators are "dielectrics".
All heatsinks are good thermal conductors.
Yet in solids, it can be expensive to have both as good characteristics.
Phase change materials that turn fluid under pressure to make a possible solution.
CPU's tend to use ceramic-glass as the thermal top to the heatsink due to extremely flat properties.
For line voltage Triacs, Mica was the best material for 5kV pulse protection and thermal conduction with thermal grease.
Dielectrics fluids like transformer oil also good thermal insulators with the flow of heat.
Figures of merit for comparing materials Thermally conductive Insulators use;
Thermal Conductivity [W/m-K],
thickness [um], shore hardness [00],
Dielectric Strength [kV/mm] and
Thermal Impedance [˚C-cm²/W]
$fracVmm cdot frac°Ccdot mmW$ or divide by thermal conduction in $frackVmm /fracWm-K$.
Traditional solutions; have been Mica, 3M tape and some polymers tapes.
Aavid Thermalloy's best economical solution is :
Thermalsil III
uses finely woven glass cloth with a silicone elastomer binder 0.152mm thick
Dielectric Strength : 26 kV/mm
Thermal Conductivity: 0.92 W/m'C
UL 94V-0
For forced-air heat removal, it is not the CFM that counts, but is often reported, rather it is the turbulent surface air velocity that controls cooling in mean [m/s].
The product of both these parameters leads to the best material properties but not the cheapest.
$endgroup$
add a comment |
$begingroup$
Actually, there is a good solution: Aluminum. Anodized aluminum. The anodization turns the surface into Aluminum Oxide, which is an insulator. Good News: The surface area is increased to help conduct the heat to the ambient air; Bad News not a flat, smooth surface to contact the power device making the heat. Solution: Thermal Compound (aka "Grease"). Important notes: there are several processes to anodize aluminum. Most of the pretty stuff is "Class I" which is soft or "Class II" which is moderately hard. You can use Class II If there is no relative movement of the device to be cooled and it is solidly clamped to the heat sink and there are no burrs or scratches, this works well. Too many "if"s & "and"s for you? Then "Class III" anodization is what you want. It tends to be unevenly colored and the black has a brownish or purplish hue. It is almost as hard as diamonds, and pretty much scratch proof. Still needs Grease, but no insulator at reasonable voltages. The military & aerospace have used this for over 50 years, either as thin (~ 0.025") anodized washers (similar to die punched mica TO-3 insulators) or the entire enclosure (think missiles). Hard to find now-a-days and costs more than other solutions, but does the job well.
For the "grease", use silicone (not petroleum based), Aluminum Oxide (not Zinc Oxide) from Dow, Shin-Etsu, Fuji-Poly, or Saint-Gobain. The boutique silver and copper based stuff for overclocking PCs 'gamers' use is both expensive and conductive. This is OK with Class III anodization, as long as it doesn't migrate, fall, dry out, powder or flake, etc. onto the current carrying stuff (just don't use it). If you really need to couple a lot of heat with grease, Beryllium Oxide is several times better than Aluminum Oxide. Just treat it like asbestos: don't lick it, don't eat it, don't breath it in. It is a skin irritant, so wear gloves, and prepare for the onslaught of a "toxic witch hunt". These greases only need to be 0.0001" to 0.0005" thick under the device (kind of translucent). Apply with a small plastic or metal squeegee; for production volumes use a stencil (same type of stencil material as used for solder paste ~0.005" SS) and a squeegee.
I have seen heat-sinks with a thin ceramic coating in the mounting area, but the difference of Cte is an issue and can crack the thin ceramic.
Hope this helps, I got this from >40 years of wandering between electrons and electron holes.
$endgroup$
$begingroup$
Yes I agree. but I don't know the dielectric breakdown is robust for grid connected IGBT's. I have a thermal chart at the end of my answer which includes hard anodized alum.
$endgroup$
– Sunnyskyguy EE75
Apr 5 at 16:52
add a comment |
$begingroup$
Overall I suspect that avoiding "wear" in the field and consequent expensive replacement is a key reason for general applications avoiding crystalline heatsinks. Not saying that metal heatsinks never fail in the field. But generally speaking replacement of metal heatsinks in the field would be a lot cheaper and require a lot less specialized equipment compared to crystalline heatsinks.
That is at the start crystalline heatsinks would be generally expensive to machine to shape and some out right breakage would occur due thermal and mechanical stress. You might still stay within acceptable total costs if all that happened at special heatsink factory. But its not uncommon for end application manufacturers to need to trim heatsink to fit etc.
Second once in a fielded application, many heatsinks experience thermal and mechanical shock and vibration which might be outside the 100% survival rate for crystalline heatsinks. Good old metal heatsinks on the other hand can take quite a bit of abuse and flexing. Some even serve secondarily as a mechanical fastening point to the outer chassis of a larger assembly.
Also in the case of crystalline heatsinks the fasteners might become points of failure instead of the heatsink. A softer fastener would damp out vibration damage to the heatsink but instead be gradually sawed through by those same vibrations and flexing.
So crystalline heatsinks would probably become an occasional repair item in the field...assuming smart thermal shutdown and alerts. Now think what special tools are needed in the field and what sort of breakage rates might apply when your average tech tries to deal with replacement. I bet heatsinks would be something many corps, governments, and private customers would expect local techs to handle even if not circuits. Just a wrench job right?
$endgroup$
add a comment |
Your Answer
StackExchange.ifUsing("editor", function ()
return StackExchange.using("schematics", function ()
StackExchange.schematics.init();
);
, "cicuitlab");
StackExchange.ready(function()
var channelOptions =
tags: "".split(" "),
id: "135"
;
initTagRenderer("".split(" "), "".split(" "), channelOptions);
StackExchange.using("externalEditor", function()
// Have to fire editor after snippets, if snippets enabled
if (StackExchange.settings.snippets.snippetsEnabled)
StackExchange.using("snippets", function()
createEditor();
);
else
createEditor();
);
function createEditor()
StackExchange.prepareEditor(
heartbeatType: 'answer',
autoActivateHeartbeat: false,
convertImagesToLinks: false,
noModals: true,
showLowRepImageUploadWarning: true,
reputationToPostImages: null,
bindNavPrevention: true,
postfix: "",
imageUploader:
brandingHtml: "Powered by u003ca class="icon-imgur-white" href="https://imgur.com/"u003eu003c/au003e",
contentPolicyHtml: "User contributions licensed under u003ca href="https://creativecommons.org/licenses/by-sa/3.0/"u003ecc by-sa 3.0 with attribution requiredu003c/au003e u003ca href="https://stackoverflow.com/legal/content-policy"u003e(content policy)u003c/au003e",
allowUrls: true
,
onDemand: true,
discardSelector: ".discard-answer"
,immediatelyShowMarkdownHelp:true
);
);
Sign up or log in
StackExchange.ready(function ()
StackExchange.helpers.onClickDraftSave('#login-link');
);
Sign up using Google
Sign up using Facebook
Sign up using Email and Password
Post as a guest
Required, but never shown
StackExchange.ready(
function ()
StackExchange.openid.initPostLogin('.new-post-login', 'https%3a%2f%2felectronics.stackexchange.com%2fquestions%2f430721%2fwhy-are-electrically-insulating-heatsinks-so-rare-is-it-just-cost%23new-answer', 'question_page');
);
Post as a guest
Required, but never shown
8 Answers
8
active
oldest
votes
8 Answers
8
active
oldest
votes
active
oldest
votes
active
oldest
votes
$begingroup$
One thing that other answers don't seem to have covered is that you only need a very thin layer of electrical insulator (at modest voltages) while the heat spreader part of a heat sink works best if it's thick. So it's more efficient to use a thin electrically-insulating barrier followed by a thick, cheap, and easily-made metal heatsink than it would be to use a single piece of a material that's thermally conductive and electrically insulating. The few materials that do exist (such as diamond) can't be extruded or otherwise easily formed into a heatsink shape. Some can be sintered but sintering can't generally reach the thermal conductivity of bulk material. The engineering effect of all this materials science is that we end up doing what we've always done.
Another factor is stock policies: by stocking bulky robust heatsinks and a smaller number (as they're not always required) of small delicate insulating pads your stock occupies less storage space and capital than if you stocked two types of bulky heatsink. Cost and performance are both better without the insulator when it's not required.
$endgroup$
10
$begingroup$
Now you've got me thinking that "extruded diamond" would be a good bit of technobabble in a sci-fi novel.
$endgroup$
– Hearth
Apr 4 at 21:48
$begingroup$
Chris thickness helps heat flow away from the interface but at the interface surface area, thinner is better for thermal resistance but electrically thicker is better so they are conflicting requirements and the product of thermal and electrical resistance is the figure of merit needed but then puncture resistance is a third factor with surface roughness. all of which makes Mica good but also hard anodized with grease
$endgroup$
– Sunnyskyguy EE75
Apr 5 at 2:38
$begingroup$
@Sunnyskyguy if the heatsink is made of one material, thicker is always better. An interface layer of not great thermal material needs to be thin
$endgroup$
– Chris H
Apr 5 at 7:24
$begingroup$
... Or rather, thicker is always better for the spreader plate part that distributes the heat to the fins
$endgroup$
– Chris H
Apr 5 at 8:47
$begingroup$
The question here is about the Electrical insulating thermal conducting interface rather than the heat spreader. The product of these two conflicting parameters (of thermal and dielectric impedance) is what makes it rare which has conflicting requirements for this layer to be thermally thin and electrically thick. So the heat spreader after this layer is not relevant to the question yet important overall
$endgroup$
– Sunnyskyguy EE75
Apr 5 at 16:14
|
show 2 more comments
$begingroup$
One thing that other answers don't seem to have covered is that you only need a very thin layer of electrical insulator (at modest voltages) while the heat spreader part of a heat sink works best if it's thick. So it's more efficient to use a thin electrically-insulating barrier followed by a thick, cheap, and easily-made metal heatsink than it would be to use a single piece of a material that's thermally conductive and electrically insulating. The few materials that do exist (such as diamond) can't be extruded or otherwise easily formed into a heatsink shape. Some can be sintered but sintering can't generally reach the thermal conductivity of bulk material. The engineering effect of all this materials science is that we end up doing what we've always done.
Another factor is stock policies: by stocking bulky robust heatsinks and a smaller number (as they're not always required) of small delicate insulating pads your stock occupies less storage space and capital than if you stocked two types of bulky heatsink. Cost and performance are both better without the insulator when it's not required.
$endgroup$
10
$begingroup$
Now you've got me thinking that "extruded diamond" would be a good bit of technobabble in a sci-fi novel.
$endgroup$
– Hearth
Apr 4 at 21:48
$begingroup$
Chris thickness helps heat flow away from the interface but at the interface surface area, thinner is better for thermal resistance but electrically thicker is better so they are conflicting requirements and the product of thermal and electrical resistance is the figure of merit needed but then puncture resistance is a third factor with surface roughness. all of which makes Mica good but also hard anodized with grease
$endgroup$
– Sunnyskyguy EE75
Apr 5 at 2:38
$begingroup$
@Sunnyskyguy if the heatsink is made of one material, thicker is always better. An interface layer of not great thermal material needs to be thin
$endgroup$
– Chris H
Apr 5 at 7:24
$begingroup$
... Or rather, thicker is always better for the spreader plate part that distributes the heat to the fins
$endgroup$
– Chris H
Apr 5 at 8:47
$begingroup$
The question here is about the Electrical insulating thermal conducting interface rather than the heat spreader. The product of these two conflicting parameters (of thermal and dielectric impedance) is what makes it rare which has conflicting requirements for this layer to be thermally thin and electrically thick. So the heat spreader after this layer is not relevant to the question yet important overall
$endgroup$
– Sunnyskyguy EE75
Apr 5 at 16:14
|
show 2 more comments
$begingroup$
One thing that other answers don't seem to have covered is that you only need a very thin layer of electrical insulator (at modest voltages) while the heat spreader part of a heat sink works best if it's thick. So it's more efficient to use a thin electrically-insulating barrier followed by a thick, cheap, and easily-made metal heatsink than it would be to use a single piece of a material that's thermally conductive and electrically insulating. The few materials that do exist (such as diamond) can't be extruded or otherwise easily formed into a heatsink shape. Some can be sintered but sintering can't generally reach the thermal conductivity of bulk material. The engineering effect of all this materials science is that we end up doing what we've always done.
Another factor is stock policies: by stocking bulky robust heatsinks and a smaller number (as they're not always required) of small delicate insulating pads your stock occupies less storage space and capital than if you stocked two types of bulky heatsink. Cost and performance are both better without the insulator when it's not required.
$endgroup$
One thing that other answers don't seem to have covered is that you only need a very thin layer of electrical insulator (at modest voltages) while the heat spreader part of a heat sink works best if it's thick. So it's more efficient to use a thin electrically-insulating barrier followed by a thick, cheap, and easily-made metal heatsink than it would be to use a single piece of a material that's thermally conductive and electrically insulating. The few materials that do exist (such as diamond) can't be extruded or otherwise easily formed into a heatsink shape. Some can be sintered but sintering can't generally reach the thermal conductivity of bulk material. The engineering effect of all this materials science is that we end up doing what we've always done.
Another factor is stock policies: by stocking bulky robust heatsinks and a smaller number (as they're not always required) of small delicate insulating pads your stock occupies less storage space and capital than if you stocked two types of bulky heatsink. Cost and performance are both better without the insulator when it's not required.
edited Apr 5 at 8:51
answered Apr 4 at 15:53
Chris HChris H
1,269612
1,269612
10
$begingroup$
Now you've got me thinking that "extruded diamond" would be a good bit of technobabble in a sci-fi novel.
$endgroup$
– Hearth
Apr 4 at 21:48
$begingroup$
Chris thickness helps heat flow away from the interface but at the interface surface area, thinner is better for thermal resistance but electrically thicker is better so they are conflicting requirements and the product of thermal and electrical resistance is the figure of merit needed but then puncture resistance is a third factor with surface roughness. all of which makes Mica good but also hard anodized with grease
$endgroup$
– Sunnyskyguy EE75
Apr 5 at 2:38
$begingroup$
@Sunnyskyguy if the heatsink is made of one material, thicker is always better. An interface layer of not great thermal material needs to be thin
$endgroup$
– Chris H
Apr 5 at 7:24
$begingroup$
... Or rather, thicker is always better for the spreader plate part that distributes the heat to the fins
$endgroup$
– Chris H
Apr 5 at 8:47
$begingroup$
The question here is about the Electrical insulating thermal conducting interface rather than the heat spreader. The product of these two conflicting parameters (of thermal and dielectric impedance) is what makes it rare which has conflicting requirements for this layer to be thermally thin and electrically thick. So the heat spreader after this layer is not relevant to the question yet important overall
$endgroup$
– Sunnyskyguy EE75
Apr 5 at 16:14
|
show 2 more comments
10
$begingroup$
Now you've got me thinking that "extruded diamond" would be a good bit of technobabble in a sci-fi novel.
$endgroup$
– Hearth
Apr 4 at 21:48
$begingroup$
Chris thickness helps heat flow away from the interface but at the interface surface area, thinner is better for thermal resistance but electrically thicker is better so they are conflicting requirements and the product of thermal and electrical resistance is the figure of merit needed but then puncture resistance is a third factor with surface roughness. all of which makes Mica good but also hard anodized with grease
$endgroup$
– Sunnyskyguy EE75
Apr 5 at 2:38
$begingroup$
@Sunnyskyguy if the heatsink is made of one material, thicker is always better. An interface layer of not great thermal material needs to be thin
$endgroup$
– Chris H
Apr 5 at 7:24
$begingroup$
... Or rather, thicker is always better for the spreader plate part that distributes the heat to the fins
$endgroup$
– Chris H
Apr 5 at 8:47
$begingroup$
The question here is about the Electrical insulating thermal conducting interface rather than the heat spreader. The product of these two conflicting parameters (of thermal and dielectric impedance) is what makes it rare which has conflicting requirements for this layer to be thermally thin and electrically thick. So the heat spreader after this layer is not relevant to the question yet important overall
$endgroup$
– Sunnyskyguy EE75
Apr 5 at 16:14
10
10
$begingroup$
Now you've got me thinking that "extruded diamond" would be a good bit of technobabble in a sci-fi novel.
$endgroup$
– Hearth
Apr 4 at 21:48
$begingroup$
Now you've got me thinking that "extruded diamond" would be a good bit of technobabble in a sci-fi novel.
$endgroup$
– Hearth
Apr 4 at 21:48
$begingroup$
Chris thickness helps heat flow away from the interface but at the interface surface area, thinner is better for thermal resistance but electrically thicker is better so they are conflicting requirements and the product of thermal and electrical resistance is the figure of merit needed but then puncture resistance is a third factor with surface roughness. all of which makes Mica good but also hard anodized with grease
$endgroup$
– Sunnyskyguy EE75
Apr 5 at 2:38
$begingroup$
Chris thickness helps heat flow away from the interface but at the interface surface area, thinner is better for thermal resistance but electrically thicker is better so they are conflicting requirements and the product of thermal and electrical resistance is the figure of merit needed but then puncture resistance is a third factor with surface roughness. all of which makes Mica good but also hard anodized with grease
$endgroup$
– Sunnyskyguy EE75
Apr 5 at 2:38
$begingroup$
@Sunnyskyguy if the heatsink is made of one material, thicker is always better. An interface layer of not great thermal material needs to be thin
$endgroup$
– Chris H
Apr 5 at 7:24
$begingroup$
@Sunnyskyguy if the heatsink is made of one material, thicker is always better. An interface layer of not great thermal material needs to be thin
$endgroup$
– Chris H
Apr 5 at 7:24
$begingroup$
... Or rather, thicker is always better for the spreader plate part that distributes the heat to the fins
$endgroup$
– Chris H
Apr 5 at 8:47
$begingroup$
... Or rather, thicker is always better for the spreader plate part that distributes the heat to the fins
$endgroup$
– Chris H
Apr 5 at 8:47
$begingroup$
The question here is about the Electrical insulating thermal conducting interface rather than the heat spreader. The product of these two conflicting parameters (of thermal and dielectric impedance) is what makes it rare which has conflicting requirements for this layer to be thermally thin and electrically thick. So the heat spreader after this layer is not relevant to the question yet important overall
$endgroup$
– Sunnyskyguy EE75
Apr 5 at 16:14
$begingroup$
The question here is about the Electrical insulating thermal conducting interface rather than the heat spreader. The product of these two conflicting parameters (of thermal and dielectric impedance) is what makes it rare which has conflicting requirements for this layer to be thermally thin and electrically thick. So the heat spreader after this layer is not relevant to the question yet important overall
$endgroup$
– Sunnyskyguy EE75
Apr 5 at 16:14
|
show 2 more comments
$begingroup$
This is hardly a new problem; those of us of a certain age remember the heatsinks with mica insulators for the TO-220 and TO-3 packages.
The issue (at the time) was both material cost and availability and materials science. We have come a long way in our understanding of thermal conductivity of various compounds over the years, but it is still relatively new technology (there are things such as thermally conductive pads that have been around for decades but are not really heat sinks in their own right).
The TO-220 has the heat spreader on the collector / drain of the device, which is usually at an elevated voltage, so the typical arrangement used this technique:
Source.
It was not unusual to use some thermal paste as well to maximise the heat transfer.
Now that does not really explain the relative rarity of integrated insulated heatsinks; that really comes down to 'is it necessary' or can I simply use the well known method of a heat sink and an electrically insulating barrier material which is less expensive (at least, it is today).
The old tried and true method has served well for many decades, but for some applications (particularly those in small devices) such a solution may well not fit.
There are quite a few offerings available, but they tend to be a bit more expensive (on a per watt basis). There is also a lot of research into other materials.
Of course, for the bling factor, you could use these.
So it comes down to a number of things and cost is a major driver. I will also note that a large market for heat sinks is for CPUs and GPUs where the case of the IC is electrically insulated anyway.
$endgroup$
add a comment |
$begingroup$
This is hardly a new problem; those of us of a certain age remember the heatsinks with mica insulators for the TO-220 and TO-3 packages.
The issue (at the time) was both material cost and availability and materials science. We have come a long way in our understanding of thermal conductivity of various compounds over the years, but it is still relatively new technology (there are things such as thermally conductive pads that have been around for decades but are not really heat sinks in their own right).
The TO-220 has the heat spreader on the collector / drain of the device, which is usually at an elevated voltage, so the typical arrangement used this technique:
Source.
It was not unusual to use some thermal paste as well to maximise the heat transfer.
Now that does not really explain the relative rarity of integrated insulated heatsinks; that really comes down to 'is it necessary' or can I simply use the well known method of a heat sink and an electrically insulating barrier material which is less expensive (at least, it is today).
The old tried and true method has served well for many decades, but for some applications (particularly those in small devices) such a solution may well not fit.
There are quite a few offerings available, but they tend to be a bit more expensive (on a per watt basis). There is also a lot of research into other materials.
Of course, for the bling factor, you could use these.
So it comes down to a number of things and cost is a major driver. I will also note that a large market for heat sinks is for CPUs and GPUs where the case of the IC is electrically insulated anyway.
$endgroup$
add a comment |
$begingroup$
This is hardly a new problem; those of us of a certain age remember the heatsinks with mica insulators for the TO-220 and TO-3 packages.
The issue (at the time) was both material cost and availability and materials science. We have come a long way in our understanding of thermal conductivity of various compounds over the years, but it is still relatively new technology (there are things such as thermally conductive pads that have been around for decades but are not really heat sinks in their own right).
The TO-220 has the heat spreader on the collector / drain of the device, which is usually at an elevated voltage, so the typical arrangement used this technique:
Source.
It was not unusual to use some thermal paste as well to maximise the heat transfer.
Now that does not really explain the relative rarity of integrated insulated heatsinks; that really comes down to 'is it necessary' or can I simply use the well known method of a heat sink and an electrically insulating barrier material which is less expensive (at least, it is today).
The old tried and true method has served well for many decades, but for some applications (particularly those in small devices) such a solution may well not fit.
There are quite a few offerings available, but they tend to be a bit more expensive (on a per watt basis). There is also a lot of research into other materials.
Of course, for the bling factor, you could use these.
So it comes down to a number of things and cost is a major driver. I will also note that a large market for heat sinks is for CPUs and GPUs where the case of the IC is electrically insulated anyway.
$endgroup$
This is hardly a new problem; those of us of a certain age remember the heatsinks with mica insulators for the TO-220 and TO-3 packages.
The issue (at the time) was both material cost and availability and materials science. We have come a long way in our understanding of thermal conductivity of various compounds over the years, but it is still relatively new technology (there are things such as thermally conductive pads that have been around for decades but are not really heat sinks in their own right).
The TO-220 has the heat spreader on the collector / drain of the device, which is usually at an elevated voltage, so the typical arrangement used this technique:
Source.
It was not unusual to use some thermal paste as well to maximise the heat transfer.
Now that does not really explain the relative rarity of integrated insulated heatsinks; that really comes down to 'is it necessary' or can I simply use the well known method of a heat sink and an electrically insulating barrier material which is less expensive (at least, it is today).
The old tried and true method has served well for many decades, but for some applications (particularly those in small devices) such a solution may well not fit.
There are quite a few offerings available, but they tend to be a bit more expensive (on a per watt basis). There is also a lot of research into other materials.
Of course, for the bling factor, you could use these.
So it comes down to a number of things and cost is a major driver. I will also note that a large market for heat sinks is for CPUs and GPUs where the case of the IC is electrically insulated anyway.
answered Apr 4 at 14:24
Peter SmithPeter Smith
15.1k11240
15.1k11240
add a comment |
add a comment |
$begingroup$
Polymer heatsinks deserve a mention. Polymer heatsinks aren't that uncommon. I come across polymer heat sinks industrial, automotive, prosumer goods once in a while. They are often hard to recognize as heatsinks, because they can have a second mechanical purposes (an enclosure, a bracket, a reflector of a lamp). These heat sinks are always custom injection-molded parts.
Polymers have a small heat conductivity, compared to any metal. This prompts a question: how can a polymer make an acceptable heatsink? In some cases, the thermal resistance of the heatsink becomes dominated by transfer from heatsink to air, rather than by conduction within the heatsink itself. This can happen when dumping heat into air with natural convection. In these cases, a heatsink made of a special polymer with a relatively high thermal conduction ( $ mathrm20 frac W mcdot K $ ) can be comparable to an aluminium ( $ mathrm200 frac W mcdot K $ ) heatsink with the same geometry.
E2 is the plastic (source)
Some additional discussion in this old answer.
$endgroup$
6
$begingroup$
On first thought, a polymer heat sink seems inefficient due to poor heat conductivity. However, its emissivity is much higher than most metals so what it lacks in conductivity it partly makes up for in radiative cooling. Disclaimer: i work for a company which produces a polymer compound for such applications.
$endgroup$
– nluigi
Apr 4 at 20:00
3
$begingroup$
@user71659 For a while, I though so too. Then I had a chance to ask one company who sells thermally conductive polymer. Their answer had surprised me. It wasn't a relatively common polymer with a thermally conductive solid filler. The polymer itself was thermally conductive. They didn't divulge what family of polymer it was. A problem with solid fillers is that it makes a plastic more viscous and difficult to injection mold (especially when there's a lot of filler by volume).
$endgroup$
– Nick Alexeev♦
Apr 5 at 0:18
1
$begingroup$
@NickAlexeev I suspect they're just trying to pull marketing BS on you. Thermally conductive polymers are filled, see this manufacturer, and 3M's fillers
$endgroup$
– user71659
Apr 5 at 0:41
1
$begingroup$
Unfilled epoxy has ~10x the TC of air so in a situation where convection isn't your friend even that can help. Filled epoxies(https://www.masterbond.com/properties/thermally-conductive-epoxy-adhesives) are a couple of orders of magnitude better. The casting method makes a difference too as epoxy-casting at atmospheric pressure tends to include bubbles of air, making for a much worse TC; a vacuum approach (where suitable) helps with that. [Filled nylon is another approach
$endgroup$
– Chris H
Apr 5 at 8:31
1
$begingroup$
@nluigi So that would make them good for applications where you're expecting a fairly constant amount of heat to remove with limited space which probably applies to many non-mechanical cases - but in cases where you have sudden large amounts but for a relatively short time, it would fail. Interesting. Never thought about heatsinks in this way!
$endgroup$
– UKMonkey
Apr 5 at 11:07
|
show 2 more comments
$begingroup$
Polymer heatsinks deserve a mention. Polymer heatsinks aren't that uncommon. I come across polymer heat sinks industrial, automotive, prosumer goods once in a while. They are often hard to recognize as heatsinks, because they can have a second mechanical purposes (an enclosure, a bracket, a reflector of a lamp). These heat sinks are always custom injection-molded parts.
Polymers have a small heat conductivity, compared to any metal. This prompts a question: how can a polymer make an acceptable heatsink? In some cases, the thermal resistance of the heatsink becomes dominated by transfer from heatsink to air, rather than by conduction within the heatsink itself. This can happen when dumping heat into air with natural convection. In these cases, a heatsink made of a special polymer with a relatively high thermal conduction ( $ mathrm20 frac W mcdot K $ ) can be comparable to an aluminium ( $ mathrm200 frac W mcdot K $ ) heatsink with the same geometry.
E2 is the plastic (source)
Some additional discussion in this old answer.
$endgroup$
6
$begingroup$
On first thought, a polymer heat sink seems inefficient due to poor heat conductivity. However, its emissivity is much higher than most metals so what it lacks in conductivity it partly makes up for in radiative cooling. Disclaimer: i work for a company which produces a polymer compound for such applications.
$endgroup$
– nluigi
Apr 4 at 20:00
3
$begingroup$
@user71659 For a while, I though so too. Then I had a chance to ask one company who sells thermally conductive polymer. Their answer had surprised me. It wasn't a relatively common polymer with a thermally conductive solid filler. The polymer itself was thermally conductive. They didn't divulge what family of polymer it was. A problem with solid fillers is that it makes a plastic more viscous and difficult to injection mold (especially when there's a lot of filler by volume).
$endgroup$
– Nick Alexeev♦
Apr 5 at 0:18
1
$begingroup$
@NickAlexeev I suspect they're just trying to pull marketing BS on you. Thermally conductive polymers are filled, see this manufacturer, and 3M's fillers
$endgroup$
– user71659
Apr 5 at 0:41
1
$begingroup$
Unfilled epoxy has ~10x the TC of air so in a situation where convection isn't your friend even that can help. Filled epoxies(https://www.masterbond.com/properties/thermally-conductive-epoxy-adhesives) are a couple of orders of magnitude better. The casting method makes a difference too as epoxy-casting at atmospheric pressure tends to include bubbles of air, making for a much worse TC; a vacuum approach (where suitable) helps with that. [Filled nylon is another approach
$endgroup$
– Chris H
Apr 5 at 8:31
1
$begingroup$
@nluigi So that would make them good for applications where you're expecting a fairly constant amount of heat to remove with limited space which probably applies to many non-mechanical cases - but in cases where you have sudden large amounts but for a relatively short time, it would fail. Interesting. Never thought about heatsinks in this way!
$endgroup$
– UKMonkey
Apr 5 at 11:07
|
show 2 more comments
$begingroup$
Polymer heatsinks deserve a mention. Polymer heatsinks aren't that uncommon. I come across polymer heat sinks industrial, automotive, prosumer goods once in a while. They are often hard to recognize as heatsinks, because they can have a second mechanical purposes (an enclosure, a bracket, a reflector of a lamp). These heat sinks are always custom injection-molded parts.
Polymers have a small heat conductivity, compared to any metal. This prompts a question: how can a polymer make an acceptable heatsink? In some cases, the thermal resistance of the heatsink becomes dominated by transfer from heatsink to air, rather than by conduction within the heatsink itself. This can happen when dumping heat into air with natural convection. In these cases, a heatsink made of a special polymer with a relatively high thermal conduction ( $ mathrm20 frac W mcdot K $ ) can be comparable to an aluminium ( $ mathrm200 frac W mcdot K $ ) heatsink with the same geometry.
E2 is the plastic (source)
Some additional discussion in this old answer.
$endgroup$
Polymer heatsinks deserve a mention. Polymer heatsinks aren't that uncommon. I come across polymer heat sinks industrial, automotive, prosumer goods once in a while. They are often hard to recognize as heatsinks, because they can have a second mechanical purposes (an enclosure, a bracket, a reflector of a lamp). These heat sinks are always custom injection-molded parts.
Polymers have a small heat conductivity, compared to any metal. This prompts a question: how can a polymer make an acceptable heatsink? In some cases, the thermal resistance of the heatsink becomes dominated by transfer from heatsink to air, rather than by conduction within the heatsink itself. This can happen when dumping heat into air with natural convection. In these cases, a heatsink made of a special polymer with a relatively high thermal conduction ( $ mathrm20 frac W mcdot K $ ) can be comparable to an aluminium ( $ mathrm200 frac W mcdot K $ ) heatsink with the same geometry.
E2 is the plastic (source)
Some additional discussion in this old answer.
edited Apr 4 at 23:18
answered Apr 4 at 17:29
Nick Alexeev♦Nick Alexeev
32.6k1066167
32.6k1066167
6
$begingroup$
On first thought, a polymer heat sink seems inefficient due to poor heat conductivity. However, its emissivity is much higher than most metals so what it lacks in conductivity it partly makes up for in radiative cooling. Disclaimer: i work for a company which produces a polymer compound for such applications.
$endgroup$
– nluigi
Apr 4 at 20:00
3
$begingroup$
@user71659 For a while, I though so too. Then I had a chance to ask one company who sells thermally conductive polymer. Their answer had surprised me. It wasn't a relatively common polymer with a thermally conductive solid filler. The polymer itself was thermally conductive. They didn't divulge what family of polymer it was. A problem with solid fillers is that it makes a plastic more viscous and difficult to injection mold (especially when there's a lot of filler by volume).
$endgroup$
– Nick Alexeev♦
Apr 5 at 0:18
1
$begingroup$
@NickAlexeev I suspect they're just trying to pull marketing BS on you. Thermally conductive polymers are filled, see this manufacturer, and 3M's fillers
$endgroup$
– user71659
Apr 5 at 0:41
1
$begingroup$
Unfilled epoxy has ~10x the TC of air so in a situation where convection isn't your friend even that can help. Filled epoxies(https://www.masterbond.com/properties/thermally-conductive-epoxy-adhesives) are a couple of orders of magnitude better. The casting method makes a difference too as epoxy-casting at atmospheric pressure tends to include bubbles of air, making for a much worse TC; a vacuum approach (where suitable) helps with that. [Filled nylon is another approach
$endgroup$
– Chris H
Apr 5 at 8:31
1
$begingroup$
@nluigi So that would make them good for applications where you're expecting a fairly constant amount of heat to remove with limited space which probably applies to many non-mechanical cases - but in cases where you have sudden large amounts but for a relatively short time, it would fail. Interesting. Never thought about heatsinks in this way!
$endgroup$
– UKMonkey
Apr 5 at 11:07
|
show 2 more comments
6
$begingroup$
On first thought, a polymer heat sink seems inefficient due to poor heat conductivity. However, its emissivity is much higher than most metals so what it lacks in conductivity it partly makes up for in radiative cooling. Disclaimer: i work for a company which produces a polymer compound for such applications.
$endgroup$
– nluigi
Apr 4 at 20:00
3
$begingroup$
@user71659 For a while, I though so too. Then I had a chance to ask one company who sells thermally conductive polymer. Their answer had surprised me. It wasn't a relatively common polymer with a thermally conductive solid filler. The polymer itself was thermally conductive. They didn't divulge what family of polymer it was. A problem with solid fillers is that it makes a plastic more viscous and difficult to injection mold (especially when there's a lot of filler by volume).
$endgroup$
– Nick Alexeev♦
Apr 5 at 0:18
1
$begingroup$
@NickAlexeev I suspect they're just trying to pull marketing BS on you. Thermally conductive polymers are filled, see this manufacturer, and 3M's fillers
$endgroup$
– user71659
Apr 5 at 0:41
1
$begingroup$
Unfilled epoxy has ~10x the TC of air so in a situation where convection isn't your friend even that can help. Filled epoxies(https://www.masterbond.com/properties/thermally-conductive-epoxy-adhesives) are a couple of orders of magnitude better. The casting method makes a difference too as epoxy-casting at atmospheric pressure tends to include bubbles of air, making for a much worse TC; a vacuum approach (where suitable) helps with that. [Filled nylon is another approach
$endgroup$
– Chris H
Apr 5 at 8:31
1
$begingroup$
@nluigi So that would make them good for applications where you're expecting a fairly constant amount of heat to remove with limited space which probably applies to many non-mechanical cases - but in cases where you have sudden large amounts but for a relatively short time, it would fail. Interesting. Never thought about heatsinks in this way!
$endgroup$
– UKMonkey
Apr 5 at 11:07
6
6
$begingroup$
On first thought, a polymer heat sink seems inefficient due to poor heat conductivity. However, its emissivity is much higher than most metals so what it lacks in conductivity it partly makes up for in radiative cooling. Disclaimer: i work for a company which produces a polymer compound for such applications.
$endgroup$
– nluigi
Apr 4 at 20:00
$begingroup$
On first thought, a polymer heat sink seems inefficient due to poor heat conductivity. However, its emissivity is much higher than most metals so what it lacks in conductivity it partly makes up for in radiative cooling. Disclaimer: i work for a company which produces a polymer compound for such applications.
$endgroup$
– nluigi
Apr 4 at 20:00
3
3
$begingroup$
@user71659 For a while, I though so too. Then I had a chance to ask one company who sells thermally conductive polymer. Their answer had surprised me. It wasn't a relatively common polymer with a thermally conductive solid filler. The polymer itself was thermally conductive. They didn't divulge what family of polymer it was. A problem with solid fillers is that it makes a plastic more viscous and difficult to injection mold (especially when there's a lot of filler by volume).
$endgroup$
– Nick Alexeev♦
Apr 5 at 0:18
$begingroup$
@user71659 For a while, I though so too. Then I had a chance to ask one company who sells thermally conductive polymer. Their answer had surprised me. It wasn't a relatively common polymer with a thermally conductive solid filler. The polymer itself was thermally conductive. They didn't divulge what family of polymer it was. A problem with solid fillers is that it makes a plastic more viscous and difficult to injection mold (especially when there's a lot of filler by volume).
$endgroup$
– Nick Alexeev♦
Apr 5 at 0:18
1
1
$begingroup$
@NickAlexeev I suspect they're just trying to pull marketing BS on you. Thermally conductive polymers are filled, see this manufacturer, and 3M's fillers
$endgroup$
– user71659
Apr 5 at 0:41
$begingroup$
@NickAlexeev I suspect they're just trying to pull marketing BS on you. Thermally conductive polymers are filled, see this manufacturer, and 3M's fillers
$endgroup$
– user71659
Apr 5 at 0:41
1
1
$begingroup$
Unfilled epoxy has ~10x the TC of air so in a situation where convection isn't your friend even that can help. Filled epoxies(https://www.masterbond.com/properties/thermally-conductive-epoxy-adhesives) are a couple of orders of magnitude better. The casting method makes a difference too as epoxy-casting at atmospheric pressure tends to include bubbles of air, making for a much worse TC; a vacuum approach (where suitable) helps with that. [Filled nylon is another approach
$endgroup$
– Chris H
Apr 5 at 8:31
$begingroup$
Unfilled epoxy has ~10x the TC of air so in a situation where convection isn't your friend even that can help. Filled epoxies(https://www.masterbond.com/properties/thermally-conductive-epoxy-adhesives) are a couple of orders of magnitude better. The casting method makes a difference too as epoxy-casting at atmospheric pressure tends to include bubbles of air, making for a much worse TC; a vacuum approach (where suitable) helps with that. [Filled nylon is another approach
$endgroup$
– Chris H
Apr 5 at 8:31
1
1
$begingroup$
@nluigi So that would make them good for applications where you're expecting a fairly constant amount of heat to remove with limited space which probably applies to many non-mechanical cases - but in cases where you have sudden large amounts but for a relatively short time, it would fail. Interesting. Never thought about heatsinks in this way!
$endgroup$
– UKMonkey
Apr 5 at 11:07
$begingroup$
@nluigi So that would make them good for applications where you're expecting a fairly constant amount of heat to remove with limited space which probably applies to many non-mechanical cases - but in cases where you have sudden large amounts but for a relatively short time, it would fail. Interesting. Never thought about heatsinks in this way!
$endgroup$
– UKMonkey
Apr 5 at 11:07
|
show 2 more comments
$begingroup$
The thing about a heat sink is that there are only really two ways to ultimately dispose of the heat, conduction and radiation.
So ultimately, assuming your emmisivity is reasonably close to 1 (Only really matters if you can run HOT, power loss to radiation is 4th power of absolute temperature), and you can make the thing have good thermal contact with the surrounding cooling media (Air, water, whatever), what you make it from only matters a little (That interface is the killer for performance, not the bulk thermal conductivity of the heatsink).
Now clearly you need to design the heatsink so that heat travels thru it reasonably efficiently and in the area where there is a lot of power flux density that might argue for something other then ally, for the bulk of the thing where you have plenty of metal to keep delta T low, cheapest is best.
For a heat spreader or insulating washer it is different of course, heat spreaders by definition are used where the power flux density is very high and minimal thermal resistance is a very good thing, hence the usual use of copper in this role.
For the insulator you do see exotic materials used, because a good thermal conductor that is also an electrical insulator is not that common, so Boron Nitride, Alumina, Beryllium Oxide(!) and the like all see service here, and I would not be shocked by someone using diamond (Probably in some weird RF device).
$endgroup$
$begingroup$
What I'm getting from this is that it's generally better to have a small insulating interface between the device and a metal heatsink, rather than making the entire heatsink insulating, is that correct? That would make sense, and probably meets the needs of most cases where insulated heatsinks would be needed.
$endgroup$
– Hearth
Apr 4 at 13:54
1
$begingroup$
More that thermally conducting but electrically insulating materials are generally less thermally conducting then metals (and more expensive/harder to machine), so the best tradeoff is usually to use the cheap, easy metal for the big bit. This is something of a compromise as it adds at least one thermal junction which adds resistance, but all engineering is compromise.
$endgroup$
– Dan Mills
Apr 4 at 13:57
$begingroup$
Diamond is four times more thermally conductive that any other material. So diamond über alles.
$endgroup$
– jonk
Apr 4 at 14:34
$begingroup$
Also should mention convection heat removal. Different from radiation and conduction. It is kind of related to conduction, though you already knew that :)
$endgroup$
– Marla
Apr 4 at 14:49
1
$begingroup$
Diamond is certainly used as an electrically-insulating, thermally-conducting layer inside experimental RF devices (and weird ones if that's how you refer to GaN). Here's a paper by some current and former colleagues of mine - spoiler: thin layers of diamond aren't great; you get nanocrystals with relatively poor thermal conductivity
$endgroup$
– Chris H
Apr 4 at 15:57
|
show 4 more comments
$begingroup$
The thing about a heat sink is that there are only really two ways to ultimately dispose of the heat, conduction and radiation.
So ultimately, assuming your emmisivity is reasonably close to 1 (Only really matters if you can run HOT, power loss to radiation is 4th power of absolute temperature), and you can make the thing have good thermal contact with the surrounding cooling media (Air, water, whatever), what you make it from only matters a little (That interface is the killer for performance, not the bulk thermal conductivity of the heatsink).
Now clearly you need to design the heatsink so that heat travels thru it reasonably efficiently and in the area where there is a lot of power flux density that might argue for something other then ally, for the bulk of the thing where you have plenty of metal to keep delta T low, cheapest is best.
For a heat spreader or insulating washer it is different of course, heat spreaders by definition are used where the power flux density is very high and minimal thermal resistance is a very good thing, hence the usual use of copper in this role.
For the insulator you do see exotic materials used, because a good thermal conductor that is also an electrical insulator is not that common, so Boron Nitride, Alumina, Beryllium Oxide(!) and the like all see service here, and I would not be shocked by someone using diamond (Probably in some weird RF device).
$endgroup$
$begingroup$
What I'm getting from this is that it's generally better to have a small insulating interface between the device and a metal heatsink, rather than making the entire heatsink insulating, is that correct? That would make sense, and probably meets the needs of most cases where insulated heatsinks would be needed.
$endgroup$
– Hearth
Apr 4 at 13:54
1
$begingroup$
More that thermally conducting but electrically insulating materials are generally less thermally conducting then metals (and more expensive/harder to machine), so the best tradeoff is usually to use the cheap, easy metal for the big bit. This is something of a compromise as it adds at least one thermal junction which adds resistance, but all engineering is compromise.
$endgroup$
– Dan Mills
Apr 4 at 13:57
$begingroup$
Diamond is four times more thermally conductive that any other material. So diamond über alles.
$endgroup$
– jonk
Apr 4 at 14:34
$begingroup$
Also should mention convection heat removal. Different from radiation and conduction. It is kind of related to conduction, though you already knew that :)
$endgroup$
– Marla
Apr 4 at 14:49
1
$begingroup$
Diamond is certainly used as an electrically-insulating, thermally-conducting layer inside experimental RF devices (and weird ones if that's how you refer to GaN). Here's a paper by some current and former colleagues of mine - spoiler: thin layers of diamond aren't great; you get nanocrystals with relatively poor thermal conductivity
$endgroup$
– Chris H
Apr 4 at 15:57
|
show 4 more comments
$begingroup$
The thing about a heat sink is that there are only really two ways to ultimately dispose of the heat, conduction and radiation.
So ultimately, assuming your emmisivity is reasonably close to 1 (Only really matters if you can run HOT, power loss to radiation is 4th power of absolute temperature), and you can make the thing have good thermal contact with the surrounding cooling media (Air, water, whatever), what you make it from only matters a little (That interface is the killer for performance, not the bulk thermal conductivity of the heatsink).
Now clearly you need to design the heatsink so that heat travels thru it reasonably efficiently and in the area where there is a lot of power flux density that might argue for something other then ally, for the bulk of the thing where you have plenty of metal to keep delta T low, cheapest is best.
For a heat spreader or insulating washer it is different of course, heat spreaders by definition are used where the power flux density is very high and minimal thermal resistance is a very good thing, hence the usual use of copper in this role.
For the insulator you do see exotic materials used, because a good thermal conductor that is also an electrical insulator is not that common, so Boron Nitride, Alumina, Beryllium Oxide(!) and the like all see service here, and I would not be shocked by someone using diamond (Probably in some weird RF device).
$endgroup$
The thing about a heat sink is that there are only really two ways to ultimately dispose of the heat, conduction and radiation.
So ultimately, assuming your emmisivity is reasonably close to 1 (Only really matters if you can run HOT, power loss to radiation is 4th power of absolute temperature), and you can make the thing have good thermal contact with the surrounding cooling media (Air, water, whatever), what you make it from only matters a little (That interface is the killer for performance, not the bulk thermal conductivity of the heatsink).
Now clearly you need to design the heatsink so that heat travels thru it reasonably efficiently and in the area where there is a lot of power flux density that might argue for something other then ally, for the bulk of the thing where you have plenty of metal to keep delta T low, cheapest is best.
For a heat spreader or insulating washer it is different of course, heat spreaders by definition are used where the power flux density is very high and minimal thermal resistance is a very good thing, hence the usual use of copper in this role.
For the insulator you do see exotic materials used, because a good thermal conductor that is also an electrical insulator is not that common, so Boron Nitride, Alumina, Beryllium Oxide(!) and the like all see service here, and I would not be shocked by someone using diamond (Probably in some weird RF device).
answered Apr 4 at 13:49
Dan MillsDan Mills
12.3k11225
12.3k11225
$begingroup$
What I'm getting from this is that it's generally better to have a small insulating interface between the device and a metal heatsink, rather than making the entire heatsink insulating, is that correct? That would make sense, and probably meets the needs of most cases where insulated heatsinks would be needed.
$endgroup$
– Hearth
Apr 4 at 13:54
1
$begingroup$
More that thermally conducting but electrically insulating materials are generally less thermally conducting then metals (and more expensive/harder to machine), so the best tradeoff is usually to use the cheap, easy metal for the big bit. This is something of a compromise as it adds at least one thermal junction which adds resistance, but all engineering is compromise.
$endgroup$
– Dan Mills
Apr 4 at 13:57
$begingroup$
Diamond is four times more thermally conductive that any other material. So diamond über alles.
$endgroup$
– jonk
Apr 4 at 14:34
$begingroup$
Also should mention convection heat removal. Different from radiation and conduction. It is kind of related to conduction, though you already knew that :)
$endgroup$
– Marla
Apr 4 at 14:49
1
$begingroup$
Diamond is certainly used as an electrically-insulating, thermally-conducting layer inside experimental RF devices (and weird ones if that's how you refer to GaN). Here's a paper by some current and former colleagues of mine - spoiler: thin layers of diamond aren't great; you get nanocrystals with relatively poor thermal conductivity
$endgroup$
– Chris H
Apr 4 at 15:57
|
show 4 more comments
$begingroup$
What I'm getting from this is that it's generally better to have a small insulating interface between the device and a metal heatsink, rather than making the entire heatsink insulating, is that correct? That would make sense, and probably meets the needs of most cases where insulated heatsinks would be needed.
$endgroup$
– Hearth
Apr 4 at 13:54
1
$begingroup$
More that thermally conducting but electrically insulating materials are generally less thermally conducting then metals (and more expensive/harder to machine), so the best tradeoff is usually to use the cheap, easy metal for the big bit. This is something of a compromise as it adds at least one thermal junction which adds resistance, but all engineering is compromise.
$endgroup$
– Dan Mills
Apr 4 at 13:57
$begingroup$
Diamond is four times more thermally conductive that any other material. So diamond über alles.
$endgroup$
– jonk
Apr 4 at 14:34
$begingroup$
Also should mention convection heat removal. Different from radiation and conduction. It is kind of related to conduction, though you already knew that :)
$endgroup$
– Marla
Apr 4 at 14:49
1
$begingroup$
Diamond is certainly used as an electrically-insulating, thermally-conducting layer inside experimental RF devices (and weird ones if that's how you refer to GaN). Here's a paper by some current and former colleagues of mine - spoiler: thin layers of diamond aren't great; you get nanocrystals with relatively poor thermal conductivity
$endgroup$
– Chris H
Apr 4 at 15:57
$begingroup$
What I'm getting from this is that it's generally better to have a small insulating interface between the device and a metal heatsink, rather than making the entire heatsink insulating, is that correct? That would make sense, and probably meets the needs of most cases where insulated heatsinks would be needed.
$endgroup$
– Hearth
Apr 4 at 13:54
$begingroup$
What I'm getting from this is that it's generally better to have a small insulating interface between the device and a metal heatsink, rather than making the entire heatsink insulating, is that correct? That would make sense, and probably meets the needs of most cases where insulated heatsinks would be needed.
$endgroup$
– Hearth
Apr 4 at 13:54
1
1
$begingroup$
More that thermally conducting but electrically insulating materials are generally less thermally conducting then metals (and more expensive/harder to machine), so the best tradeoff is usually to use the cheap, easy metal for the big bit. This is something of a compromise as it adds at least one thermal junction which adds resistance, but all engineering is compromise.
$endgroup$
– Dan Mills
Apr 4 at 13:57
$begingroup$
More that thermally conducting but electrically insulating materials are generally less thermally conducting then metals (and more expensive/harder to machine), so the best tradeoff is usually to use the cheap, easy metal for the big bit. This is something of a compromise as it adds at least one thermal junction which adds resistance, but all engineering is compromise.
$endgroup$
– Dan Mills
Apr 4 at 13:57
$begingroup$
Diamond is four times more thermally conductive that any other material. So diamond über alles.
$endgroup$
– jonk
Apr 4 at 14:34
$begingroup$
Diamond is four times more thermally conductive that any other material. So diamond über alles.
$endgroup$
– jonk
Apr 4 at 14:34
$begingroup$
Also should mention convection heat removal. Different from radiation and conduction. It is kind of related to conduction, though you already knew that :)
$endgroup$
– Marla
Apr 4 at 14:49
$begingroup$
Also should mention convection heat removal. Different from radiation and conduction. It is kind of related to conduction, though you already knew that :)
$endgroup$
– Marla
Apr 4 at 14:49
1
1
$begingroup$
Diamond is certainly used as an electrically-insulating, thermally-conducting layer inside experimental RF devices (and weird ones if that's how you refer to GaN). Here's a paper by some current and former colleagues of mine - spoiler: thin layers of diamond aren't great; you get nanocrystals with relatively poor thermal conductivity
$endgroup$
– Chris H
Apr 4 at 15:57
$begingroup$
Diamond is certainly used as an electrically-insulating, thermally-conducting layer inside experimental RF devices (and weird ones if that's how you refer to GaN). Here's a paper by some current and former colleagues of mine - spoiler: thin layers of diamond aren't great; you get nanocrystals with relatively poor thermal conductivity
$endgroup$
– Chris H
Apr 4 at 15:57
|
show 4 more comments
$begingroup$
From a technical standpoint its certainly possible to manufacture heatsinks with built in isolator pads. The reason they don't do it is economics.
Between the different mechanical, electrical, and thermal choices there are a lot of different combinations. If the isolator and heatsink were one part then the vendors would have to stock a lot more unique part numbers.
By factoring out the isolator and heat sink into unique products the user has a lot more choices.
Here are some of the things to consider.
1) In many cases the user will use gap pads between heat-sinks and hot components to pick up slack in mechanical tolerances. This means that each user will want the pad to be a different thickness.
2) Thermal isolator pad materials vary in how well they are able to conform to rough surfaces. There is often a trade between how squishy the material is and how well it conducts heat.
3) Different users will have different isolation requirements in terms of voltage. There is a trade off between isolation voltage, the material thickness and the thermal resistance.
3) Adding an insulator between a heat-sink and a part has a penalty in terms of thermal resistance. If its possible to not use an insulating layer then you will get the best thermal performance in that case.
$endgroup$
$begingroup$
While this is a good answer, the question I asked was more about heatsinks made entirely of one electrically-insulating substance--not ones with an insulator attached to them.
$endgroup$
– Hearth
Apr 4 at 21:45
add a comment |
$begingroup$
From a technical standpoint its certainly possible to manufacture heatsinks with built in isolator pads. The reason they don't do it is economics.
Between the different mechanical, electrical, and thermal choices there are a lot of different combinations. If the isolator and heatsink were one part then the vendors would have to stock a lot more unique part numbers.
By factoring out the isolator and heat sink into unique products the user has a lot more choices.
Here are some of the things to consider.
1) In many cases the user will use gap pads between heat-sinks and hot components to pick up slack in mechanical tolerances. This means that each user will want the pad to be a different thickness.
2) Thermal isolator pad materials vary in how well they are able to conform to rough surfaces. There is often a trade between how squishy the material is and how well it conducts heat.
3) Different users will have different isolation requirements in terms of voltage. There is a trade off between isolation voltage, the material thickness and the thermal resistance.
3) Adding an insulator between a heat-sink and a part has a penalty in terms of thermal resistance. If its possible to not use an insulating layer then you will get the best thermal performance in that case.
$endgroup$
$begingroup$
While this is a good answer, the question I asked was more about heatsinks made entirely of one electrically-insulating substance--not ones with an insulator attached to them.
$endgroup$
– Hearth
Apr 4 at 21:45
add a comment |
$begingroup$
From a technical standpoint its certainly possible to manufacture heatsinks with built in isolator pads. The reason they don't do it is economics.
Between the different mechanical, electrical, and thermal choices there are a lot of different combinations. If the isolator and heatsink were one part then the vendors would have to stock a lot more unique part numbers.
By factoring out the isolator and heat sink into unique products the user has a lot more choices.
Here are some of the things to consider.
1) In many cases the user will use gap pads between heat-sinks and hot components to pick up slack in mechanical tolerances. This means that each user will want the pad to be a different thickness.
2) Thermal isolator pad materials vary in how well they are able to conform to rough surfaces. There is often a trade between how squishy the material is and how well it conducts heat.
3) Different users will have different isolation requirements in terms of voltage. There is a trade off between isolation voltage, the material thickness and the thermal resistance.
3) Adding an insulator between a heat-sink and a part has a penalty in terms of thermal resistance. If its possible to not use an insulating layer then you will get the best thermal performance in that case.
$endgroup$
From a technical standpoint its certainly possible to manufacture heatsinks with built in isolator pads. The reason they don't do it is economics.
Between the different mechanical, electrical, and thermal choices there are a lot of different combinations. If the isolator and heatsink were one part then the vendors would have to stock a lot more unique part numbers.
By factoring out the isolator and heat sink into unique products the user has a lot more choices.
Here are some of the things to consider.
1) In many cases the user will use gap pads between heat-sinks and hot components to pick up slack in mechanical tolerances. This means that each user will want the pad to be a different thickness.
2) Thermal isolator pad materials vary in how well they are able to conform to rough surfaces. There is often a trade between how squishy the material is and how well it conducts heat.
3) Different users will have different isolation requirements in terms of voltage. There is a trade off between isolation voltage, the material thickness and the thermal resistance.
3) Adding an insulator between a heat-sink and a part has a penalty in terms of thermal resistance. If its possible to not use an insulating layer then you will get the best thermal performance in that case.
edited Apr 4 at 16:50
answered Apr 4 at 16:41
user4574user4574
3,672512
3,672512
$begingroup$
While this is a good answer, the question I asked was more about heatsinks made entirely of one electrically-insulating substance--not ones with an insulator attached to them.
$endgroup$
– Hearth
Apr 4 at 21:45
add a comment |
$begingroup$
While this is a good answer, the question I asked was more about heatsinks made entirely of one electrically-insulating substance--not ones with an insulator attached to them.
$endgroup$
– Hearth
Apr 4 at 21:45
$begingroup$
While this is a good answer, the question I asked was more about heatsinks made entirely of one electrically-insulating substance--not ones with an insulator attached to them.
$endgroup$
– Hearth
Apr 4 at 21:45
$begingroup$
While this is a good answer, the question I asked was more about heatsinks made entirely of one electrically-insulating substance--not ones with an insulator attached to them.
$endgroup$
– Hearth
Apr 4 at 21:45
add a comment |
$begingroup$
The best compromise is to make an extremely thin large surface area layer with a high rated Voltage [kV/mm] with sufficient hardness to not be cut or punctured but must also be low cost.
Thermally conductive insulator characteristics include;
Cost-effective
Resistant to tears and cut-through
High dielectric strength
UL94 VO rated options available
Low ageing rate: Pads do not dry out, ooze out or crack
Gap Filling, if burrs, roughness or planarity is a problem
Compatibility (gas sensors must be non-silicone and LED interfaces must be non-organic)
Low dielectric constant for capacitance load on collector/drain tabs on high dV/dt high voltage drivers
All electrical insulators are "dielectrics".
All heatsinks are good thermal conductors.
Yet in solids, it can be expensive to have both as good characteristics.
Phase change materials that turn fluid under pressure to make a possible solution.
CPU's tend to use ceramic-glass as the thermal top to the heatsink due to extremely flat properties.
For line voltage Triacs, Mica was the best material for 5kV pulse protection and thermal conduction with thermal grease.
Dielectrics fluids like transformer oil also good thermal insulators with the flow of heat.
Figures of merit for comparing materials Thermally conductive Insulators use;
Thermal Conductivity [W/m-K],
thickness [um], shore hardness [00],
Dielectric Strength [kV/mm] and
Thermal Impedance [˚C-cm²/W]
$fracVmm cdot frac°Ccdot mmW$ or divide by thermal conduction in $frackVmm /fracWm-K$.
Traditional solutions; have been Mica, 3M tape and some polymers tapes.
Aavid Thermalloy's best economical solution is :
Thermalsil III
uses finely woven glass cloth with a silicone elastomer binder 0.152mm thick
Dielectric Strength : 26 kV/mm
Thermal Conductivity: 0.92 W/m'C
UL 94V-0
For forced-air heat removal, it is not the CFM that counts, but is often reported, rather it is the turbulent surface air velocity that controls cooling in mean [m/s].
The product of both these parameters leads to the best material properties but not the cheapest.
$endgroup$
add a comment |
$begingroup$
The best compromise is to make an extremely thin large surface area layer with a high rated Voltage [kV/mm] with sufficient hardness to not be cut or punctured but must also be low cost.
Thermally conductive insulator characteristics include;
Cost-effective
Resistant to tears and cut-through
High dielectric strength
UL94 VO rated options available
Low ageing rate: Pads do not dry out, ooze out or crack
Gap Filling, if burrs, roughness or planarity is a problem
Compatibility (gas sensors must be non-silicone and LED interfaces must be non-organic)
Low dielectric constant for capacitance load on collector/drain tabs on high dV/dt high voltage drivers
All electrical insulators are "dielectrics".
All heatsinks are good thermal conductors.
Yet in solids, it can be expensive to have both as good characteristics.
Phase change materials that turn fluid under pressure to make a possible solution.
CPU's tend to use ceramic-glass as the thermal top to the heatsink due to extremely flat properties.
For line voltage Triacs, Mica was the best material for 5kV pulse protection and thermal conduction with thermal grease.
Dielectrics fluids like transformer oil also good thermal insulators with the flow of heat.
Figures of merit for comparing materials Thermally conductive Insulators use;
Thermal Conductivity [W/m-K],
thickness [um], shore hardness [00],
Dielectric Strength [kV/mm] and
Thermal Impedance [˚C-cm²/W]
$fracVmm cdot frac°Ccdot mmW$ or divide by thermal conduction in $frackVmm /fracWm-K$.
Traditional solutions; have been Mica, 3M tape and some polymers tapes.
Aavid Thermalloy's best economical solution is :
Thermalsil III
uses finely woven glass cloth with a silicone elastomer binder 0.152mm thick
Dielectric Strength : 26 kV/mm
Thermal Conductivity: 0.92 W/m'C
UL 94V-0
For forced-air heat removal, it is not the CFM that counts, but is often reported, rather it is the turbulent surface air velocity that controls cooling in mean [m/s].
The product of both these parameters leads to the best material properties but not the cheapest.
$endgroup$
add a comment |
$begingroup$
The best compromise is to make an extremely thin large surface area layer with a high rated Voltage [kV/mm] with sufficient hardness to not be cut or punctured but must also be low cost.
Thermally conductive insulator characteristics include;
Cost-effective
Resistant to tears and cut-through
High dielectric strength
UL94 VO rated options available
Low ageing rate: Pads do not dry out, ooze out or crack
Gap Filling, if burrs, roughness or planarity is a problem
Compatibility (gas sensors must be non-silicone and LED interfaces must be non-organic)
Low dielectric constant for capacitance load on collector/drain tabs on high dV/dt high voltage drivers
All electrical insulators are "dielectrics".
All heatsinks are good thermal conductors.
Yet in solids, it can be expensive to have both as good characteristics.
Phase change materials that turn fluid under pressure to make a possible solution.
CPU's tend to use ceramic-glass as the thermal top to the heatsink due to extremely flat properties.
For line voltage Triacs, Mica was the best material for 5kV pulse protection and thermal conduction with thermal grease.
Dielectrics fluids like transformer oil also good thermal insulators with the flow of heat.
Figures of merit for comparing materials Thermally conductive Insulators use;
Thermal Conductivity [W/m-K],
thickness [um], shore hardness [00],
Dielectric Strength [kV/mm] and
Thermal Impedance [˚C-cm²/W]
$fracVmm cdot frac°Ccdot mmW$ or divide by thermal conduction in $frackVmm /fracWm-K$.
Traditional solutions; have been Mica, 3M tape and some polymers tapes.
Aavid Thermalloy's best economical solution is :
Thermalsil III
uses finely woven glass cloth with a silicone elastomer binder 0.152mm thick
Dielectric Strength : 26 kV/mm
Thermal Conductivity: 0.92 W/m'C
UL 94V-0
For forced-air heat removal, it is not the CFM that counts, but is often reported, rather it is the turbulent surface air velocity that controls cooling in mean [m/s].
The product of both these parameters leads to the best material properties but not the cheapest.
$endgroup$
The best compromise is to make an extremely thin large surface area layer with a high rated Voltage [kV/mm] with sufficient hardness to not be cut or punctured but must also be low cost.
Thermally conductive insulator characteristics include;
Cost-effective
Resistant to tears and cut-through
High dielectric strength
UL94 VO rated options available
Low ageing rate: Pads do not dry out, ooze out or crack
Gap Filling, if burrs, roughness or planarity is a problem
Compatibility (gas sensors must be non-silicone and LED interfaces must be non-organic)
Low dielectric constant for capacitance load on collector/drain tabs on high dV/dt high voltage drivers
All electrical insulators are "dielectrics".
All heatsinks are good thermal conductors.
Yet in solids, it can be expensive to have both as good characteristics.
Phase change materials that turn fluid under pressure to make a possible solution.
CPU's tend to use ceramic-glass as the thermal top to the heatsink due to extremely flat properties.
For line voltage Triacs, Mica was the best material for 5kV pulse protection and thermal conduction with thermal grease.
Dielectrics fluids like transformer oil also good thermal insulators with the flow of heat.
Figures of merit for comparing materials Thermally conductive Insulators use;
Thermal Conductivity [W/m-K],
thickness [um], shore hardness [00],
Dielectric Strength [kV/mm] and
Thermal Impedance [˚C-cm²/W]
$fracVmm cdot frac°Ccdot mmW$ or divide by thermal conduction in $frackVmm /fracWm-K$.
Traditional solutions; have been Mica, 3M tape and some polymers tapes.
Aavid Thermalloy's best economical solution is :
Thermalsil III
uses finely woven glass cloth with a silicone elastomer binder 0.152mm thick
Dielectric Strength : 26 kV/mm
Thermal Conductivity: 0.92 W/m'C
UL 94V-0
For forced-air heat removal, it is not the CFM that counts, but is often reported, rather it is the turbulent surface air velocity that controls cooling in mean [m/s].
The product of both these parameters leads to the best material properties but not the cheapest.
edited Apr 5 at 3:59
answered Apr 5 at 3:17


Sunnyskyguy EE75Sunnyskyguy EE75
72k227103
72k227103
add a comment |
add a comment |
$begingroup$
Actually, there is a good solution: Aluminum. Anodized aluminum. The anodization turns the surface into Aluminum Oxide, which is an insulator. Good News: The surface area is increased to help conduct the heat to the ambient air; Bad News not a flat, smooth surface to contact the power device making the heat. Solution: Thermal Compound (aka "Grease"). Important notes: there are several processes to anodize aluminum. Most of the pretty stuff is "Class I" which is soft or "Class II" which is moderately hard. You can use Class II If there is no relative movement of the device to be cooled and it is solidly clamped to the heat sink and there are no burrs or scratches, this works well. Too many "if"s & "and"s for you? Then "Class III" anodization is what you want. It tends to be unevenly colored and the black has a brownish or purplish hue. It is almost as hard as diamonds, and pretty much scratch proof. Still needs Grease, but no insulator at reasonable voltages. The military & aerospace have used this for over 50 years, either as thin (~ 0.025") anodized washers (similar to die punched mica TO-3 insulators) or the entire enclosure (think missiles). Hard to find now-a-days and costs more than other solutions, but does the job well.
For the "grease", use silicone (not petroleum based), Aluminum Oxide (not Zinc Oxide) from Dow, Shin-Etsu, Fuji-Poly, or Saint-Gobain. The boutique silver and copper based stuff for overclocking PCs 'gamers' use is both expensive and conductive. This is OK with Class III anodization, as long as it doesn't migrate, fall, dry out, powder or flake, etc. onto the current carrying stuff (just don't use it). If you really need to couple a lot of heat with grease, Beryllium Oxide is several times better than Aluminum Oxide. Just treat it like asbestos: don't lick it, don't eat it, don't breath it in. It is a skin irritant, so wear gloves, and prepare for the onslaught of a "toxic witch hunt". These greases only need to be 0.0001" to 0.0005" thick under the device (kind of translucent). Apply with a small plastic or metal squeegee; for production volumes use a stencil (same type of stencil material as used for solder paste ~0.005" SS) and a squeegee.
I have seen heat-sinks with a thin ceramic coating in the mounting area, but the difference of Cte is an issue and can crack the thin ceramic.
Hope this helps, I got this from >40 years of wandering between electrons and electron holes.
$endgroup$
$begingroup$
Yes I agree. but I don't know the dielectric breakdown is robust for grid connected IGBT's. I have a thermal chart at the end of my answer which includes hard anodized alum.
$endgroup$
– Sunnyskyguy EE75
Apr 5 at 16:52
add a comment |
$begingroup$
Actually, there is a good solution: Aluminum. Anodized aluminum. The anodization turns the surface into Aluminum Oxide, which is an insulator. Good News: The surface area is increased to help conduct the heat to the ambient air; Bad News not a flat, smooth surface to contact the power device making the heat. Solution: Thermal Compound (aka "Grease"). Important notes: there are several processes to anodize aluminum. Most of the pretty stuff is "Class I" which is soft or "Class II" which is moderately hard. You can use Class II If there is no relative movement of the device to be cooled and it is solidly clamped to the heat sink and there are no burrs or scratches, this works well. Too many "if"s & "and"s for you? Then "Class III" anodization is what you want. It tends to be unevenly colored and the black has a brownish or purplish hue. It is almost as hard as diamonds, and pretty much scratch proof. Still needs Grease, but no insulator at reasonable voltages. The military & aerospace have used this for over 50 years, either as thin (~ 0.025") anodized washers (similar to die punched mica TO-3 insulators) or the entire enclosure (think missiles). Hard to find now-a-days and costs more than other solutions, but does the job well.
For the "grease", use silicone (not petroleum based), Aluminum Oxide (not Zinc Oxide) from Dow, Shin-Etsu, Fuji-Poly, or Saint-Gobain. The boutique silver and copper based stuff for overclocking PCs 'gamers' use is both expensive and conductive. This is OK with Class III anodization, as long as it doesn't migrate, fall, dry out, powder or flake, etc. onto the current carrying stuff (just don't use it). If you really need to couple a lot of heat with grease, Beryllium Oxide is several times better than Aluminum Oxide. Just treat it like asbestos: don't lick it, don't eat it, don't breath it in. It is a skin irritant, so wear gloves, and prepare for the onslaught of a "toxic witch hunt". These greases only need to be 0.0001" to 0.0005" thick under the device (kind of translucent). Apply with a small plastic or metal squeegee; for production volumes use a stencil (same type of stencil material as used for solder paste ~0.005" SS) and a squeegee.
I have seen heat-sinks with a thin ceramic coating in the mounting area, but the difference of Cte is an issue and can crack the thin ceramic.
Hope this helps, I got this from >40 years of wandering between electrons and electron holes.
$endgroup$
$begingroup$
Yes I agree. but I don't know the dielectric breakdown is robust for grid connected IGBT's. I have a thermal chart at the end of my answer which includes hard anodized alum.
$endgroup$
– Sunnyskyguy EE75
Apr 5 at 16:52
add a comment |
$begingroup$
Actually, there is a good solution: Aluminum. Anodized aluminum. The anodization turns the surface into Aluminum Oxide, which is an insulator. Good News: The surface area is increased to help conduct the heat to the ambient air; Bad News not a flat, smooth surface to contact the power device making the heat. Solution: Thermal Compound (aka "Grease"). Important notes: there are several processes to anodize aluminum. Most of the pretty stuff is "Class I" which is soft or "Class II" which is moderately hard. You can use Class II If there is no relative movement of the device to be cooled and it is solidly clamped to the heat sink and there are no burrs or scratches, this works well. Too many "if"s & "and"s for you? Then "Class III" anodization is what you want. It tends to be unevenly colored and the black has a brownish or purplish hue. It is almost as hard as diamonds, and pretty much scratch proof. Still needs Grease, but no insulator at reasonable voltages. The military & aerospace have used this for over 50 years, either as thin (~ 0.025") anodized washers (similar to die punched mica TO-3 insulators) or the entire enclosure (think missiles). Hard to find now-a-days and costs more than other solutions, but does the job well.
For the "grease", use silicone (not petroleum based), Aluminum Oxide (not Zinc Oxide) from Dow, Shin-Etsu, Fuji-Poly, or Saint-Gobain. The boutique silver and copper based stuff for overclocking PCs 'gamers' use is both expensive and conductive. This is OK with Class III anodization, as long as it doesn't migrate, fall, dry out, powder or flake, etc. onto the current carrying stuff (just don't use it). If you really need to couple a lot of heat with grease, Beryllium Oxide is several times better than Aluminum Oxide. Just treat it like asbestos: don't lick it, don't eat it, don't breath it in. It is a skin irritant, so wear gloves, and prepare for the onslaught of a "toxic witch hunt". These greases only need to be 0.0001" to 0.0005" thick under the device (kind of translucent). Apply with a small plastic or metal squeegee; for production volumes use a stencil (same type of stencil material as used for solder paste ~0.005" SS) and a squeegee.
I have seen heat-sinks with a thin ceramic coating in the mounting area, but the difference of Cte is an issue and can crack the thin ceramic.
Hope this helps, I got this from >40 years of wandering between electrons and electron holes.
$endgroup$
Actually, there is a good solution: Aluminum. Anodized aluminum. The anodization turns the surface into Aluminum Oxide, which is an insulator. Good News: The surface area is increased to help conduct the heat to the ambient air; Bad News not a flat, smooth surface to contact the power device making the heat. Solution: Thermal Compound (aka "Grease"). Important notes: there are several processes to anodize aluminum. Most of the pretty stuff is "Class I" which is soft or "Class II" which is moderately hard. You can use Class II If there is no relative movement of the device to be cooled and it is solidly clamped to the heat sink and there are no burrs or scratches, this works well. Too many "if"s & "and"s for you? Then "Class III" anodization is what you want. It tends to be unevenly colored and the black has a brownish or purplish hue. It is almost as hard as diamonds, and pretty much scratch proof. Still needs Grease, but no insulator at reasonable voltages. The military & aerospace have used this for over 50 years, either as thin (~ 0.025") anodized washers (similar to die punched mica TO-3 insulators) or the entire enclosure (think missiles). Hard to find now-a-days and costs more than other solutions, but does the job well.
For the "grease", use silicone (not petroleum based), Aluminum Oxide (not Zinc Oxide) from Dow, Shin-Etsu, Fuji-Poly, or Saint-Gobain. The boutique silver and copper based stuff for overclocking PCs 'gamers' use is both expensive and conductive. This is OK with Class III anodization, as long as it doesn't migrate, fall, dry out, powder or flake, etc. onto the current carrying stuff (just don't use it). If you really need to couple a lot of heat with grease, Beryllium Oxide is several times better than Aluminum Oxide. Just treat it like asbestos: don't lick it, don't eat it, don't breath it in. It is a skin irritant, so wear gloves, and prepare for the onslaught of a "toxic witch hunt". These greases only need to be 0.0001" to 0.0005" thick under the device (kind of translucent). Apply with a small plastic or metal squeegee; for production volumes use a stencil (same type of stencil material as used for solder paste ~0.005" SS) and a squeegee.
I have seen heat-sinks with a thin ceramic coating in the mounting area, but the difference of Cte is an issue and can crack the thin ceramic.
Hope this helps, I got this from >40 years of wandering between electrons and electron holes.
answered Apr 5 at 6:49
Imre A CsaszarImre A Csaszar
512
512
$begingroup$
Yes I agree. but I don't know the dielectric breakdown is robust for grid connected IGBT's. I have a thermal chart at the end of my answer which includes hard anodized alum.
$endgroup$
– Sunnyskyguy EE75
Apr 5 at 16:52
add a comment |
$begingroup$
Yes I agree. but I don't know the dielectric breakdown is robust for grid connected IGBT's. I have a thermal chart at the end of my answer which includes hard anodized alum.
$endgroup$
– Sunnyskyguy EE75
Apr 5 at 16:52
$begingroup$
Yes I agree. but I don't know the dielectric breakdown is robust for grid connected IGBT's. I have a thermal chart at the end of my answer which includes hard anodized alum.
$endgroup$
– Sunnyskyguy EE75
Apr 5 at 16:52
$begingroup$
Yes I agree. but I don't know the dielectric breakdown is robust for grid connected IGBT's. I have a thermal chart at the end of my answer which includes hard anodized alum.
$endgroup$
– Sunnyskyguy EE75
Apr 5 at 16:52
add a comment |
$begingroup$
Overall I suspect that avoiding "wear" in the field and consequent expensive replacement is a key reason for general applications avoiding crystalline heatsinks. Not saying that metal heatsinks never fail in the field. But generally speaking replacement of metal heatsinks in the field would be a lot cheaper and require a lot less specialized equipment compared to crystalline heatsinks.
That is at the start crystalline heatsinks would be generally expensive to machine to shape and some out right breakage would occur due thermal and mechanical stress. You might still stay within acceptable total costs if all that happened at special heatsink factory. But its not uncommon for end application manufacturers to need to trim heatsink to fit etc.
Second once in a fielded application, many heatsinks experience thermal and mechanical shock and vibration which might be outside the 100% survival rate for crystalline heatsinks. Good old metal heatsinks on the other hand can take quite a bit of abuse and flexing. Some even serve secondarily as a mechanical fastening point to the outer chassis of a larger assembly.
Also in the case of crystalline heatsinks the fasteners might become points of failure instead of the heatsink. A softer fastener would damp out vibration damage to the heatsink but instead be gradually sawed through by those same vibrations and flexing.
So crystalline heatsinks would probably become an occasional repair item in the field...assuming smart thermal shutdown and alerts. Now think what special tools are needed in the field and what sort of breakage rates might apply when your average tech tries to deal with replacement. I bet heatsinks would be something many corps, governments, and private customers would expect local techs to handle even if not circuits. Just a wrench job right?
$endgroup$
add a comment |
$begingroup$
Overall I suspect that avoiding "wear" in the field and consequent expensive replacement is a key reason for general applications avoiding crystalline heatsinks. Not saying that metal heatsinks never fail in the field. But generally speaking replacement of metal heatsinks in the field would be a lot cheaper and require a lot less specialized equipment compared to crystalline heatsinks.
That is at the start crystalline heatsinks would be generally expensive to machine to shape and some out right breakage would occur due thermal and mechanical stress. You might still stay within acceptable total costs if all that happened at special heatsink factory. But its not uncommon for end application manufacturers to need to trim heatsink to fit etc.
Second once in a fielded application, many heatsinks experience thermal and mechanical shock and vibration which might be outside the 100% survival rate for crystalline heatsinks. Good old metal heatsinks on the other hand can take quite a bit of abuse and flexing. Some even serve secondarily as a mechanical fastening point to the outer chassis of a larger assembly.
Also in the case of crystalline heatsinks the fasteners might become points of failure instead of the heatsink. A softer fastener would damp out vibration damage to the heatsink but instead be gradually sawed through by those same vibrations and flexing.
So crystalline heatsinks would probably become an occasional repair item in the field...assuming smart thermal shutdown and alerts. Now think what special tools are needed in the field and what sort of breakage rates might apply when your average tech tries to deal with replacement. I bet heatsinks would be something many corps, governments, and private customers would expect local techs to handle even if not circuits. Just a wrench job right?
$endgroup$
add a comment |
$begingroup$
Overall I suspect that avoiding "wear" in the field and consequent expensive replacement is a key reason for general applications avoiding crystalline heatsinks. Not saying that metal heatsinks never fail in the field. But generally speaking replacement of metal heatsinks in the field would be a lot cheaper and require a lot less specialized equipment compared to crystalline heatsinks.
That is at the start crystalline heatsinks would be generally expensive to machine to shape and some out right breakage would occur due thermal and mechanical stress. You might still stay within acceptable total costs if all that happened at special heatsink factory. But its not uncommon for end application manufacturers to need to trim heatsink to fit etc.
Second once in a fielded application, many heatsinks experience thermal and mechanical shock and vibration which might be outside the 100% survival rate for crystalline heatsinks. Good old metal heatsinks on the other hand can take quite a bit of abuse and flexing. Some even serve secondarily as a mechanical fastening point to the outer chassis of a larger assembly.
Also in the case of crystalline heatsinks the fasteners might become points of failure instead of the heatsink. A softer fastener would damp out vibration damage to the heatsink but instead be gradually sawed through by those same vibrations and flexing.
So crystalline heatsinks would probably become an occasional repair item in the field...assuming smart thermal shutdown and alerts. Now think what special tools are needed in the field and what sort of breakage rates might apply when your average tech tries to deal with replacement. I bet heatsinks would be something many corps, governments, and private customers would expect local techs to handle even if not circuits. Just a wrench job right?
$endgroup$
Overall I suspect that avoiding "wear" in the field and consequent expensive replacement is a key reason for general applications avoiding crystalline heatsinks. Not saying that metal heatsinks never fail in the field. But generally speaking replacement of metal heatsinks in the field would be a lot cheaper and require a lot less specialized equipment compared to crystalline heatsinks.
That is at the start crystalline heatsinks would be generally expensive to machine to shape and some out right breakage would occur due thermal and mechanical stress. You might still stay within acceptable total costs if all that happened at special heatsink factory. But its not uncommon for end application manufacturers to need to trim heatsink to fit etc.
Second once in a fielded application, many heatsinks experience thermal and mechanical shock and vibration which might be outside the 100% survival rate for crystalline heatsinks. Good old metal heatsinks on the other hand can take quite a bit of abuse and flexing. Some even serve secondarily as a mechanical fastening point to the outer chassis of a larger assembly.
Also in the case of crystalline heatsinks the fasteners might become points of failure instead of the heatsink. A softer fastener would damp out vibration damage to the heatsink but instead be gradually sawed through by those same vibrations and flexing.
So crystalline heatsinks would probably become an occasional repair item in the field...assuming smart thermal shutdown and alerts. Now think what special tools are needed in the field and what sort of breakage rates might apply when your average tech tries to deal with replacement. I bet heatsinks would be something many corps, governments, and private customers would expect local techs to handle even if not circuits. Just a wrench job right?
edited Apr 8 at 6:05
answered Apr 8 at 5:57
NotSoSimpleNotSoSimple
112
112
add a comment |
add a comment |
Thanks for contributing an answer to Electrical Engineering Stack Exchange!
- Please be sure to answer the question. Provide details and share your research!
But avoid …
- Asking for help, clarification, or responding to other answers.
- Making statements based on opinion; back them up with references or personal experience.
Use MathJax to format equations. MathJax reference.
To learn more, see our tips on writing great answers.
Sign up or log in
StackExchange.ready(function ()
StackExchange.helpers.onClickDraftSave('#login-link');
);
Sign up using Google
Sign up using Facebook
Sign up using Email and Password
Post as a guest
Required, but never shown
StackExchange.ready(
function ()
StackExchange.openid.initPostLogin('.new-post-login', 'https%3a%2f%2felectronics.stackexchange.com%2fquestions%2f430721%2fwhy-are-electrically-insulating-heatsinks-so-rare-is-it-just-cost%23new-answer', 'question_page');
);
Post as a guest
Required, but never shown
Sign up or log in
StackExchange.ready(function ()
StackExchange.helpers.onClickDraftSave('#login-link');
);
Sign up using Google
Sign up using Facebook
Sign up using Email and Password
Post as a guest
Required, but never shown
Sign up or log in
StackExchange.ready(function ()
StackExchange.helpers.onClickDraftSave('#login-link');
);
Sign up using Google
Sign up using Facebook
Sign up using Email and Password
Post as a guest
Required, but never shown
Sign up or log in
StackExchange.ready(function ()
StackExchange.helpers.onClickDraftSave('#login-link');
);
Sign up using Google
Sign up using Facebook
Sign up using Email and Password
Sign up using Google
Sign up using Facebook
Sign up using Email and Password
Post as a guest
Required, but never shown
Required, but never shown
Required, but never shown
Required, but never shown
Required, but never shown
Required, but never shown
Required, but never shown
Required, but never shown
Required, but never shown
43uXhNCrRKFmiK2cdy nHmL6I
1
$begingroup$
@crj11 Well! I had looked around for some but didn't encounter that company. They don't give a price, but I suppose it's one of those things where if you have to ask it's too expensive.
$endgroup$
– Hearth
Apr 4 at 13:31
1
$begingroup$
I've used a beryllium oxide washer for this. Problem is that the dust is toxic. You should use gloves and masks on the assembly line to limit exposure to the dust.
$endgroup$
– stark
Apr 4 at 13:45
2
$begingroup$
@Huisman: A lot!
$endgroup$
– Peter Smith
Apr 4 at 13:45
1
$begingroup$
@stark Beryllium oxide? That's somewhat alarming! What drove the decision to use BeO instead of BN or something else less likely to cause injury?
$endgroup$
– Hearth
Apr 4 at 15:21
1
$begingroup$
@Hearth I believe it was a combination of high temp, electrical insulation, thermal conductivity, and mechanical stability. BeO is very stable once in place. Availability of information about other choices was also an issue in pre-internet days.
$endgroup$
– stark
Apr 4 at 17:40